熱処理時の割れ
変形とともに、熱処理中の「割れ」も困った問題で、過去(昭和年代)には、しばしば焼割れが発生しました。 しかし、現在では、鋼材の品質が上がったことや熱処理作業の対策などで、この焼割れトラブルは激減しています。
ただ、大きな品物で、焼入れ性の高い鋼種を使って、高い硬さが必要な場合などでは、いまでも焼割れの危険性はあります。
割れは、引張応力集中部から起こる
ここでは、焼入れ、焼き戻し、時効などで、生じる割れについて説明します。
熱処理をすることで、品物は、変態による体積変化や熱変化のために応力(品物内部の力)が加わって変形します。 その変形が大きくなりすぎると、品物の形が変形し、品物の一部の材料が持つ強さ(特に引張強さ)の降伏限界を超えると、「永久変形」になりますし、それ以上の変形が加わり、品物の一部で材料の引張強度を超えると、品物が割れたり破壊してしまいます。
言い方を変えれば、変形の大きくなった状態で「割れ」が発生すると言えます。
そして経験的には、高温では品物の硬さが下がって、粘くなっているので、割れが起きるのは、品物が硬化する、比較的低い温度の状態です。
通常の品物の熱処理では、熱による膨張収縮や、組織変化による体積が発生します。前のページの図をもう一度見てみましょう。
(再掲の図)
これは、熱処理過程の変寸の状態を示す模式図です。 昇温とともに長さが伸びます。焼入れして硬化が始まるまでは、材料は柔らかいので、問題になるのは、焼入れして硬化していく段階以降です。(青丸部分の硬化して寸法変化する段階)
焼割れは、焼入れ時点だけのものをさすのではなく、焼戻し完了までの過程に起こる割れを、便宜的に「焼割れ」という場合が多いようです。
焼入れから1回目の焼戻しまでは連続して行う場合が多いので、焼戻し後に割れているのを発見する場合が多くなっています。
この図には、長さだけの変化を示していますが、通常の品物は立体であるので、これらの変化はもっと複雑になっているでしょう。
図で、焼入れ冷却中のピンクの点線部分は、鋼は未硬化状態なので、変形はしても、応力(内部の力の不均衡)の発生は少ないのですが、青丸で囲んだ、焼入れ硬化していく過程では、変形と残留応力の増加が進んでいきます。
さらに、高い硬さが必要であれば、200℃までの低い温度の焼戻しになるので、緑の線のように、最終的には、※印の変寸と変形による内部応力がどこかに残る・・・ということになります。
ここで、J-Kは焼戻しマルテンサイトに変化する段階、M-Lは残留オーステナイトが分解する段階、M-Oは残留オーステナイトの消失での寸法変化ですが、普通の工具鋼では300℃以上の焼戻しはすることがありませんし、この図では示されていませんが、2次硬さが出る高合金鋼では、500℃を超えて、大きな長さの伸び縮みが発生します。
意外と、焼入れ性の良い、大きな品物が危険
経験で言えば、品物の温度が高い状態では割れが発生しませんし、また、水焼入れ品や小さな品物での割れはほとんど見られません。 しかし、焼入れ性の良い合金鋼で、品物が大きくなってくるとわれの危険がでてきます。
われの発生する場所(割れの起点)は、品物の応力が集中する部分で、応力の大きさが、材料の持つ降伏限を超えると、永久変形が発生し、そして、その部分で、引張強さを超えた力が品物の一部に集中すると、その部分から割れが発生しやすいといえます。
割れが発生してそれが進行していくと、ある程度の応力が開放されるので、割れは思ったほど進行しませんし、新たな割れも起こりにくくなります。
発生頻度で言えば、割れること自体が特殊なケースですから、熱処理時の焼割れが頻繁に起こるものではありません。
現在では、隅部は大きなR加工をする、鋭利な先端は面取りをしてなめらかに仕上げる、極端に薄い部分が無いようにする、・・・ などの製作設計上の注意や加工者の知識として知られていますし、また、熱処理面でも、焼入れ状態で放置しないで焼戻しをする、急激な熱変化を避ける、硬化温度域は均一にゆっくり冷やす、高い硬さにするものは、できるだけ無酸化熱処理をする・・・などの対策もあって、数kg程度の小さな品物が割れることはほとんどなくなっています。
材料が良くなって、近年は焼割れが激減
私の経験では、昭和年代では半年に1回ぐらいと、かなりの頻度で割れの不具合が起こっていた記憶があります。 当時は、小さい品物でも「焼割れ」が起きていましたし、何100kgもある大きな鍛造用の金型が、焼入れ冷却中に油から引き上げて、150℃以下になった頃から、「ピン」という大きな金属音を出して割れたり、焼戻し炉に入れるときに音がして割れるのに数回遭遇したり、炉から出て来たときに割れていた・・・というケースもしばしば経験しました。
大きな品物が焼入れによって膨張する力は、非常に大きいために、大きい品物ほど割れやすい・・・と考えるのも間違いではありませんが、私の感触では、現在の鋼材に比べると、特に工具鋼の、比較的大きな高合金鋼の材料の品位は、かなり低かったので、やはり、現在の製鋼技術が良くなったことで、焼割れが減ったという理由も大きいでしょう。
現在では、焼割れはめったに起こらないのですが、SKD11などの焼入れ性の良い材料で、厚さが80mmを超えて、外形も300mmを超える品物で、81HS(60HRC)以上の硬さを確保しようとすると、空冷する場合は、常温まで完全に冷やす・・・などの無理をしなくてはなりません。
またさらに、硬さが確実に欲しい場合はサブゼロをしたり、油冷をしたり・・・というように、さらに無理をする熱処理をしなければならないので、キーや穴の部分から割れる危険性は拭えません。
設計する側は、当然ですが、熱処理で割れることは想定していないと思うので、熱処理する側は、ヒヤヒヤものです。
焼き割れは大きな損失
「近年では、焼割れはほとんどない」と言うものの、熱処理すると、焼割れの危険性はゼロではなく、もしも「焼割れ(焼き割れ)」が起きてしまうと、熱処理業者にとっても、お客様側にとっても困りものです。
焼割れが起きると、弁償の問題がでます。 もちろん、熱処理業者が総費用のすべてを負担することはなく、建て前では、熱処理価格の3倍を補償限度としているのですが、それでは納得しないお客様もいるので、現品を調査して原因を探すこともあります。
しかし、調査の費用は膨大な割には、調査して原因が推定できるのは、経験的には1割もありませんし、たとえ材料欠陥などが見つかっても、普通の品位の鋼材であれば、材料欠陥が皆無ではないのですから、結局は、関係各社の痛み分けになります。
焼入焼戻しをすると、立方体のなどの単純な形状でも変形しますし、大きな品物になると中心部は硬さが低くなっているので、大きな引張応力が集中する部分があれば割れる可能性がゼロではありません。 そして、割れや変形は熱処理での宿命ですから、それが嫌なら熱処理はできません。
速く冷やしても割れるものでもない
焼割れは、①急激な冷却が必要な低合金鋼に生じる場合と、②ゆっくり冷却しても焼の入る高合金鋼に生じる場合があります。 近年は、②のケースのほうが焼割れは多いようです。
先にも書きましたが、割れの起点における「引張応力」が材料の持つ強さを超えることが原因で起きる・・・というのが基本的な見方・考え方ですが、全体が均一な硬さであれば、割れにくいですし、熱処理による寸法変化がなければ、当然割れることはありませんし、応力が、圧縮応力が加わる状態のところからは「割れ」が生じにくい・・・といえます。
完全焼入れ部分は膨張するのですが・・・
どのような鋼種でも、焼入れによって品物が硬化すると、トータル的に、体積は膨張します。 しかし、少し詳しく言えば、完全焼入れになる部分は体積膨張するのですが、品物の中心部になるほど、焼入れが完全でなくなるので、体積収縮するところも出てきます。
専門的に言えば、組織の状態が、マルテンサイト状態か、ベイナイト状態か、ソルバイト状態か・・・で、その部分の膨張収縮状態が変わります。
そのために生じた応力が、品物の一部に、引張応力となって集中した場合は、材料の持つ強度を超えてしまうと「変形や割れ」が生じる・・・と説明されています。
材料には「方向性」があるうえに、3次元的に均一に膨張するのではなく、形状によっては、(全体では体積が増加しますが) 一部で「収縮」する部分もでてくるので、非常に焼割れの予想はしにくいものです。
①の、焼入れ性の低い低合金鋼では、焼きが入って硬化している部分は圧縮応力のために、品物先端や角部に「割れ」が生じることは少なく、しばしば言われるような、「早く冷やすと割れる」・・・という言い方は、ほとんど正しくないと言えます。
つまり、焼入れ性の低い低合金鋼の焼入れでは、「遅く冷える、強度の弱い部分から割れやすい」ということになります。
このために、特に、奥まった隅部のR加工や、仕上げに注意することは重要で、もちろん、角部でも鋭角で薄い部分は避けるのは当然です。
②の焼入性の高いダイス鋼などの鋼種では、品物が大きくて、高い硬さが要求されるものは要注意です。
実際の熱処理では、油焼入れしなくてもいい鋼種や大型の品物であっても、硬さを高めるために、油冷をして冷却速度を上げて硬化させることも多いのですが、割れの危険性は増します。 しかし、ほとんど「簡単に割れるものではない」と考えるぐらいにしないと、熱処理自体ができないことになります。
冷却速度が早すぎると、変形は多くなる傾向はあるものの、焼割れに対しては、このような熱処理操作の問題を気にしないほうが良いでしょう。
極端な話ですが、空冷によって焼きが入るSKD11を、液体窒素や水で冷やす実験などをしても、小さい品物では、割れることはありません。
もちろん、後者の焼入れ性の高い鋼種の焼割れは、熱処理変寸などの形状的影響を受けるところが割れの起点になると考えると、品物の断面が極端に小さいところや尖った部分などは設計時点で避けるようにしなくてはいけません。
曲り対策も割れ対策も、永久に熱処理作業につきまとうことなのですが、近年は、用いられる材料の傾向が、焼入れ性の良い材料に変わってきており、急冷しなくても十分に硬化する鋼種に変わってきていますので、その点では冷却速度の調整範囲に余裕が出ることや、温度を上げて矯正しやすい・・・などで問題が起きにくくなってきています。
性能よりも変形の少ない熱処理が望まれる困った傾向
熱処理は、工具寿命を伸ばすために行うもののはずですが、お客様の要望は、良い組織よりも、曲り(歪 ・変寸)を出さないようにすることの要望のほうが多いという、困った傾向があります。
『硬さは少々低くても、曲がらないように熱処理してほしい・・・』 と要望されることが多いことなどですが、熱処理する側としては、これは困ったことです。
変形を抑えるためには、硬さや組織の状態を無視して、冷却を調整して変形対策をする場合も出てきます。
たとえば、風の当たる方向を変えたり、治具などで覆って、その部分の冷却を加減するのですが、もちろん、これは邪道で、故意に冷却速度を遅くすることは、往々にして、熱処理組織を悪くするので、「品質」的にはよくないことです。
このことをわかっていながら、お客さんの第一要求が「曲りを少なく」であれば、「品質は構わない」という、お客様の要求に沿って熱処理をしなければならないのですが、こういう矛盾を含む問題については、熱処理従事者としては頭の痛いことで、顧客の要求を満たすことが最優先であれば、これも「熱処理」ですから、仕方がないということになります。
次に、焼戻し時などに生じる変形について見ていきます。
焼戻し時の変形
焼戻しの際にも温度によって、組織変化と熱によって応力変化や応力解放が進行することは、上でも見てきましたが、焼戻しの際に、焼戻しマルテンサイトに変化したり、残留オーステナイトが変化したり、高合金鋼では二次硬化などで組織が変化するのに合わせて、体積変化生じて、内部応力が変化します。
これらの変化で品物が割れることはほとんど皆無です。 その段階で、応力は均一化される方向になるので、これを矯正(曲がり取り)に利用しています。
一般に、焼戻し温度を上昇させていくと、鋼は次第に軟化しながら応力が均一化していきます。これによって、変形量(変形の大きさ)は増える場合も減る場合もあります。
高合金鋼では500℃以上で再硬化(二次硬化)する鋼種があるので、低合金鋼とは別にこれによって、体積は変化します。
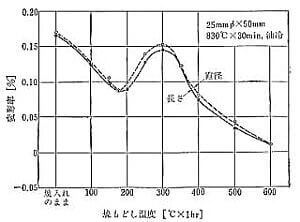
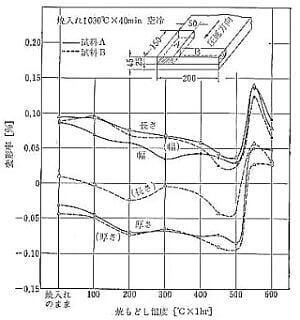
上図の左は比較的低合金の「SKS3(プロテリアル(旧:日立金属)のSGT)」の例です。 300℃付近では残留オーステナイト変化による変寸が見られます。 それ以上の温度では、ソルバイト化による変寸率の変化が生じています。 この鋼種は、通常、200℃前後の焼戻しをして使用される鋼で、変寸率が比較的小さな鋼種です。
右は高合金鋼の「SKD11(プロテリアル(旧:日立金属)のSLD)」の「焼戻し温度と変形率」の関係を示す例です。
500℃程度まではSKS3と同じ、残留オーステナイトの影響による傾向がありますが、そこから2次硬化による0.1%程度の大きな寸法変化が生じています。
SKD11は、主に、冷間で使用される工具鋼なので、ほとんどが200℃前後の焼戻しで使用されるものですから、「膨張する」としておけば、このグラフは必要ないのですが、ただ、変寸量の絶対量は別にして、このようなグラフがあれば、温度に対する変形傾向や材料に方向性がある様子などで、矯正作業の参考にできます。
注意すべき点は、このグラフは一例としてみていく必要があります。つまり、この長さ幅の方向性の変寸傾向や焼戻しによる変化は参考になりますが、鋼材の製造過程の圧延比(鍛錬比)によって、絶対値は変わりますし、さらに、実際の品物のように、厚さが厚いものになると、全く違ったグラフになります。
焼入れによって、ほとんどすべてについては、全体の体積は増えますが、この図の厚さ部分のように、寸法的に「縮む」ところが出てくることはしばしば経験しますので、充分な仕上げしろをつけておかないと、仕上げ寸法に仕上がらないということもあります。
正確な変寸量は予測困難
変寸(熱処理での組織変化に伴う体積変化)について、完全に予想することは、現状では無理です。
しばしば、熱処理依頼のお客さんで、「どれくらい寸法変化しますか?」という問い合わせをいただくことがあります。
それに対しては、 冗談に思えるかもしれませんが、「変寸の傾向は分かりますが、どうなるかは、『焼いてみないと分かりません』・・・としか答えられないほどに、変寸量や変形の予想ができないのが現状です。
上のようなグラフがあっても、品物の寸法や、鋼材の履歴(例えば、製鋼時の鋼塊からの鍛錬・圧延比や、鋼材偏析など)で変寸量は大きく変わります。
しかし、焼戻し温度における変寸傾向は変わりませんので、これら実験データは、役に立ちます。
私の勤めていた会社では、せん断刃物を作っていたので、しばしば、各製鋼メーカーさんのSKD11相当品を使って、5mもある細長い品物の焼入れをしていたのですが、+0.1%の変寸率であれば、5mでは長さ方向に5mmも穴ピッチが伸びるので、焼入れ前のピッチ修正加工が必須になります。 しかし、各社さんの材料では変寸量が一定していませんし、ロットが変わると、その変寸率も変わるので、およその予想はしますが、1mm以内に収まれば上出来です。
同時に製造されて入荷した、同サイズの鋼材では、比較的に変寸率は揃っていますので、変寸率が変わる原因は、鋼材の製造履歴(インゴットの大きさや鍛錬比、化学成分など)によっている可能性が大きい感じですから、これは使う側では、どうしようもありません。 上の変寸グラフの数値は1例としてみておくといいでしょう。
結局は、当面の対策としては、ある程度の予測による寸法修正をした上で、仕上げ代(余肉)をつけておいて、熱処理後に仕上げ加工をすることになりますし、取付穴の誤差は、設計する側が取り回しを考えなければいけないでしょう。(ただ、残念ながら、5mで±0.5mmというピッチの図面は、現実にはたくさんあって、取り付ける側では2mm程度の余裕になっているので問題はおきませんが・・・)
応力除去と矯正時の操作
変形は、「曲がり」、「歪み」などとも称されており、それを矯正(曲がりの除去)する操作は、「曲り取り」「ひずみ取り」「矯正」などと呼ばれています。
「ひずみとり」は、変形の除去以外に、「内部の偏応力の除去」という意味で用いられることがあり、これは、「低温焼なまし」「応力除去焼なまし」などをすることを指しています。
いずれも、熱処理温度の決まりはありませんが、焼戻しした品物では、その温度以上にすると硬さが低下するので、硬さをどうするのかがポイントになります。
温度を高くすると効果が高いので、硬さ範囲の余裕があれば、できるだけ高い温度に上げて矯正作業や応力除去熱処理をします。
焼入れ硬化させた後の矯正作業は、「冷間(常温)」で行う場合もありますが、硬さが高いと危険ですので、できるだけ温度を上げて行います。
熱を加えた状態では、鋼のじん性が高くなっており、高温状態での硬さも下がっているので、外力を加えても折損する危険性は低下します。
そしてさらに、焼戻し温度による組織変化を利用すると、矯正がやりやすくなります。
矯正の方法
硬さの低いものについては、油圧プレスやフリクションプレスなどをつかって、冷間で「プレス」したり、丸棒鋼では、単ロールや多ロールなどを用いて曲りを矯正します。
しかし、おおむね、外力による矯正は、30HRC程度以上の硬さになると、機械的に外力を加えるのは危険が伴います。
そのために、それ以上の高い硬さの品物は、品物を治具などで「逆反り」させて拘束して、バーナーで熱を加えて矯正する方法や、焼戻し時の組織変化を利用して、温度を上げながら、徐々に「逆反り」させて矯正する方法の他に、 焼入れ冷却中に、Ms点にかかるまでの、焼きが入っていない高い温度でプレス矯正をする方法などが行われています。
焼入れ硬化後に焼戻しをしてしまうと、その後に温度を上げても矯正の効果が薄く、1回目の焼戻しを兼ねて矯正作業を行うのが効果的です。
矯正は、弾性限を超えて力を加える必要があるので、温度を上げながら、治具などを利用して拘束する(通常は、反対方向に無理に曲げて固定して焼戻しする)方法をとります。
焼戻しを併用して矯正する場合は、焼戻し過程で起こる組織変化と硬さ変化をうまく利用するものなので、2回目以降の焼戻しでは、1回目の温度をより高温にしないと効果が出ません。 さらに、大きな硬さ低下をさせないと矯正効果がでないので、1回目の矯正チャンスを逃すと、うまくいきません。
また、いずれにしても、外力を加えて矯正しますので、その応力が残存して、その後の加工時に、それが戻ってきて「悪さ」をすることがありますが、これはある程度仕方がないことです。
つまり、矯正をした品物は、矯正の残留応力が残っているので、それがそれがあとの加工中や品物の使用中に出てきて、曲がりや形状の狂いを生じることが多々あります。
そのために、矯正後に、焼戻し温度以下の「応力除去焼なまし」を付加して、「戻り」を軽減することも行われています。
これは、応力を開放するというよりも、「ピーク応力の開放」という意味合いで行われるもので、画期的な効果は望めませんが、「応力を平均化させる処理」と考えていいでしょう。
これらの矯正作業は、すべて、余分な時間・手間・費用が掛かります。そして、矯正や応力除去が確実であるかどうかも、その時にはわからない場合も往々にしてあるし、時間が経つと変形してくることもあります。
これらの矯正や応力除去処理をすれば、完璧に曲がりのない状態になるかと言うと、それも保証できません。
【古くから行われている方法】
その他の方法として、冷間あるいは温間で、タガネやハンマーなどで品物に圧痕をつけることで局部応力を発生させて曲りをとる方法が古くからおこなわれています。
しかしこの作業は、誰にでもできるという方法ではなく、割れなどのリスクも大きく、圧痕ができるので、仕上げしろとの兼ね合いが出てきます。 一般の熱処理品にはお勧めできるものではありません。
【プレステンパー】
矯正作業で、焼戻しする時に、治具などで品物を拘束して変形を除去する方法は「プレステンパー」と称される場合があります。
また、焼入れ過程での変形をさせないようにするために、赤熱した鋼の状態で、品物を治具などで拘束して焼入れをする方法があります。
これは、「プレスクエンチ」と言われます。
これらを含めて、いずれの矯正作業も経験が必要な作業ですし、治具なども品物以上に大型になることもあり、手間と費用の掛かる作業です。
時効変形(経年変化)
熱処理時の変形は焼入れ焼戻し時に生じる以外に、品物を熱処理してから、かなりの時間を経過しながら、変化や変寸が生じることがあります。
これは時効変形や経年変化と呼ばれます。
品物が温度や時間によって変形する理由には、内部の応力が均一化する方向に進んでいくことで変形が生じることや、焼入れした品物は、長い時間を掛けて組織や硬さが変化するのは仕方がないことです(→こちらの、焼戻しパラメータを参照)。
硬さが高い状態は、内部に応力を付加している状態なので、時間が経つと、少ない量ですが、寸法や形状が変わり、変寸や変形が生じます。
鋳物などでは、鋳込み時に生じた内部の偏応力は避けられないために、経年変化を緩和するために、「枯らし」という、戸外で長期間放置する工程が取られることがあります。
この「枯らし」は、品物を長時間にわたって屋外で放置しておくという方法の他に、その代替として、低温での焼なましをして、応力を解放と変形を安定な状態にしておいてから最終の加工をするという方法です。
鋳物だけでなく、鋼の場合でも、熱処理による残留応力の不均衡や残留オーステナイトが多いと、時間がたってから寸法狂いや破損が生じる場合があります。
それを防ぐために、温度を加える焼戻し(または、応力除去焼なまし)による「オーステナイトの安定化処理」や、残留オーステナイトを低減するための 「サブゼロ処理」をすることで経年変化を低減する方法がとられます。
【サブゼロ処理】
サブゼロ処理は、0℃以下に品物を冷やす処理をいいます。(→こちらでも説明)
サブゼロ処理は、Mf点が150℃程度より低い鋼種や、残留オーステナイトが多い鋼種では、充分な硬さが得られないことがあったり、残留オーステナイトが原因で、経年変化が起こりやすいので、それを防ぐために、焼入れ後で焼戻しするまでに、炭酸ガスやドライアイスなどを用いて低温に品物を冷やして、残留オーステナイトを少なくする目的で行われるのがサブゼロ処理です。
熱処理作業は、液化炭酸ガスやドライアイスを用いて、-75℃程度に品物を冷やすことが多く行われます。
残留オーステナイトだけでなく、すべての焼入れ焼戻しした鋼は、長時間が経過すると、組織や硬さ変化が進行するのですが、それに伴って体積変化が生じて、変寸や変形が現れるのが経年変化と言われるものです。
本来、焼入れ・焼戻しは、硬さを高くして内部応力を高める処理といえますし、高合金鋼を高い硬さで使用する場合には、焼入れ時に生じる残留オーステナイトを皆無にすることは困難ですので、焼入れした品物の経年変化をなくすることは容易でありません。
書籍などにもしばしば、「サブゼロ処理によって残留オーステナイトを無くす」という表現を見かけますが、そう言い切るのは問題があります。
例えば、SKD11などは、 焼入れ時には通常は20%以上の残留オーステナイトがあって、これをなくそうと、いろいろな方法でサブゼロ処理を含む熱処理試験をしたことがありますが、5%以下にするのは大変でした。
サブゼロ処理をすることで、残留オーステナイト量を軽減することや硬さの上昇などは望めますが、残留オーステナイトをゼロにできるものと過信してはいけません。
残留オーステナイト量が多い鋼種は、それを低減することはできないとなると、経年変化を抑えることは難しいと言えます。
言い換えれば、経年変化を嫌うゲージ類などにSKD11などの残留オーステナイトが多い鋼種を使うと、たとえサブゼロ処理をしても残留オーステナイトがゼロになる保証はありませんので、 このような鋼種を使うことは適当ではないと言えます。
ちなみに、SKD11は560℃程度の高温焼戻しによって、ほぼ消失しますが、55HRC以下の硬さになってしまいますので、充分な硬さがほしいのなら、560℃の焼戻しで60HRCになるDC53やQCM8などの8%Cr系の材料などを使用するのも一つの方法です。
↑このページの上へ
R2.4 CSS変更 R2.8写真の整合化 最終確認R6.4月