熱処理時の変形
焼入れ、焼もどし、時効などの熱処理中の変形は、熱による膨張収縮と変態による寸法変化が合わさって3次元的に生じます。
この変形については、鋼の組織変化などで生じた寸法変化を「変寸(へんすん)」、製品の形状の狂いを「変形」と表現する場合が多いのですが、ここでは、両方を含んだ寸法変化を変形として説明しています。
共析鋼の熱処理変化
この図は、共析鋼(炭素量が約0.8%の鋼)の、温度に伴う長さ変化(1次元の変化)を示す例で、(a)→(b)→(c)→(d) のように、冷却速度を早くした時の長さの変化を示しています。
(a)は焼なまし、(b)は焼ならし、(c)は油焼入れ、(d)は水焼入れ・・・に対応させてみていただくといいでしょう。
全てで、温度をあげていくと膨張し、温度降下時には収縮しています。 そして、700℃前後で加熱と冷却時には、変態による変化が見られます。
焼入れ状態を示す(c)(d)では、500℃以下で、焼入れ硬化(マルテンサイト変態)によって、最終的には、元の寸法に戻らない膨張変化をしています。
(注) ここでの(b)は、元の寸法に戻っているのですが、焼なましした材料を用いて、少し冷却の早い「焼ならし」をすれば、組織の違いが生じて、元の寸法に戻りません。 ここで、それを説明すると複雑になるためか、ここでは、「焼入れのような組織変化がなければ、膨張収縮しない」としているようです。
この図は長さだけの変化ですが、熱処理をする品物で考えると、3次元的な寸法変化をするので、品物各部の体積が変化するために、品物が変形することになります。
また、高温の状態では、鋼の硬さが低下しているので、不均一な寸法変化は、簡単に品物を変形させます。 そしてさらに、変態による変形が加わって、変形が助長されます。
熱膨張・熱収縮による寸法変化
(a)の場合で、焼なましの場合のように、ゆっくり加熱してゆっくり冷却する状態を見てみましょう。
加熱にともなって、A→Bに熱膨張していき、750℃付近で、加熱時にはB→Cに、冷却時にはE→Fに見られる変態による寸法変化(A1変態)が見られますが、加熱冷却速度が遅いので、可逆的な変化になっています。
(注)この材料の元の状態は「焼なまし状態」なので、可逆的な変化になっていますが、元の組織の状態が違えば、元の状態に戻らないのは当然のことです。
この加熱冷却では、常温では体心立方晶であった結晶構造が、面心立方晶の「オーステナイト」になる時の状況を示しているのですが、加熱のときと同様に、冷却の場合でも、その逆の変態反応が生じています。
(注)この図は、わかりやすいように、冷却速度の影響を表すように図示されていますが、オーステナイト温度より高い「D」点まで温度を上げると、結晶粒の増大などの影響で、常温になった時に、元の「A」寸法に戻らない場合も生じます。一般的には、加熱すれば、何らかの影響を受けるということは、常に意識しておくといいでしょう。
これは、先にも書いたように、直線的な長さ変化を見たものですので、立体的な品物では、この寸法変化が「変形」となって現れます。
そして、実際の熱処理中(加熱冷却中)は、品物のどこでもが同じ温度になっていないために、熱膨張に差が生じて、複雑な変形が生じています。
変態による寸法変化
(c)(d)の、焼入れによって、組織が変化した場合を見ましょう。
一番下の(d)では、早い冷却による収縮傾向のあと、250℃から、膨張が見られます。これが「変態」に伴う寸法変化です。(上のグラフの「G」点は、「Ms点(マルテンサイト変態が生じ始める温度)」に対応しています)
(c)(d)のように冷却速度が早い状態は「焼入れ」操作の急冷の状態ですが、このように速い速度で常温まで冷却した場合には、元の寸法よりも長くなっていることがわかります。
しかし、実際の品物のように3次元的になる焼入れでは、不均一な各部の冷却になると、さらに品物の変形の様子が複雑になりますし、トータル的な体積膨張で、必ず元の形状に戻る可能性は少なくなります。
このように、熱処理での変形は、①熱に伴う膨張収縮と、②変態時の組織変化に伴う膨張収縮の両方が関係し、前者を「熱による変形」、 後者を「変態による変形 」と呼んでいます。
これ以外の変形に及ぼす要因
材料の方向性、機械加工時の加工による残留応力、鋼材の成分などの不均一さ、焼なましなどの熱処理不良・・・などがあり、その影響は、焼入れ加熱の時に重なって変形に影響します。(これらの原因は、頭では考えられるものの、どのような状態になっているのか把握しにくいので、対策も難しいものです)
冷却が早くなった場合を示す(c)(d)は焼入れによって「マルテンサイト」という組織が現れることによる体積変化で、このマルテンサイトが生じることで鋼が非常に硬くなります。
つまり、マルテンサイトが生じる早い冷却速度で冷却すれば、急激な熱変化とマルテンサイトの生成によって、変形量が多くなります。
焼戻し時の変形
下の図は、先の図に焼なまし時の寸法変化を加えた図です。
焼入れが完了した時点は「H」で、J→K→・・・と、再加熱して、Bに至るのですが、この図では、冷却速度が遅い「焼なまし」の場合と、冷却速度が大きい「焼入れ」の場合を合わせて書き込んであるので、見にくい図ですが、もう一度説明をします。
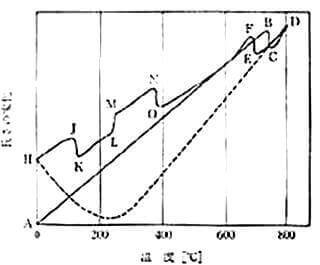
ゆっくりと加熱冷却した場合(焼入れでない場合)
Aから加熱して、B点で「オーステナイト」に変態し、その後、D点の「焼入れ温度」まで加熱した後にゆっくり冷却すると、E→Fのように「オーステナイト」から「パーライト」という組織に変態します。
そしてその後は熱収縮をしながらA点に戻ります。
焼入れが終わった時点(H点)から見ると、焼戻し過程では、寸法収縮が起こっていることになります。 そして、ゆっくりと、再度加熱すると同じような経過をたどります。
(注)この図では、あたかも、熱処理を繰り返すと、再現性があるようにしめされていますが、厳密には、結晶粒の増大などが加わって、この様になるとは限らないことをすでに説明しましたので、ここでは考え方だけを見ておいてください。
D点から急冷した場合(焼入れ硬化する場合)
ゆっくり加熱する過程は最高温度のD点までは同じですが、D点の温度から急冷すると、点線のような寸法収縮過程を経てからは、マルテンサイトが生成して体積膨張します。(この図は長さ変化を示すので、「伸び」として表現されます)
H点のように、焼入れが完了した時点では、寸法が増加しています。 これを「マルテンサイト変態による体積増加(または、寸法増大)」という言い方をします。
その状態からゆっくりと再加熱すると、Hから焼戻しによる寸法変化が加わって、JからOのように組織の変化を経てB点に至る・・・と図示されています。
【参考】 この変化については、「焼戻し」の項目で説明する内容ですが、この図の見方と考え方について簡単に注意点を含めて紹介します。
ここでは、考え方だけを示しています。 ただ、上の図の出所や詳しいデータなどは示されていないので、これらは、講習会などでの解説はほとんどないのですが、ここでは、焼戻し過程の変化を含めて説明します。
約0.8%Cの共析鋼を焼入れすることによって、H点では、「マルテンサイト」と「残留オーステナイト」という組織になっています。
それをゆっくりと再加熱するのが「焼戻し」の熱処理操作ですが、J→K→L→Mでは、マルテンサイトが焼戻しマルテンサイトに変化する過程が示されており、N→O →Bでは、「残留オーステナイトの分解」→「ソルバイトの生成」 が起こっています。
「ソルバイト」は先程の①のゆっくりした冷却時に変態で生じた「パーライト」の微細な組織・・・と説明されるのですが、「炭化物Fe3C」と「フェライト」の微細な層状組織です。(ここでは、聞き流しでいいのですが、こちらの焼戻しの項目でも説明しています)
ここで示された長さ変化は、必ずしもこのようになるとは限らないのですが、上のような2つの変化が生じていることを説明する場合にしばしば用いられることもある図です。
ただ、普通は、このような変化は単純なものではなく、もっと複雑ですし、熱を加えることによる不可逆変化のために、O点からB点につながるとは限りませんので、あくまでこの図も、説明用のものと考えておいてください。
通常の品物では、焼入れの加熱、冷却、焼戻しを経ることで、熱による変形に加えて、組織変化による寸法変化が加わるために、予想できないような変形が生じてしまう可能性もあります。
単純な形状ではない品物では、変形の傾向や変形量の予想り、傾向を把握することすら難しくなってきます。
加熱の不均一と熱膨張による変形
加熱中の品物は熱によって膨張・収縮します。
一般的な鋼の線膨張係数は、平均的に0.000011程度です。
成分や組織の状態と温度域によって、この値は若干変わりますが、この数字を頭に入れておくと良いでしょう。
例えば、0.5mの鋼製の品物を30℃から300℃に加熱すると、500(mm)x270(℃)x0.000011≒1.5(mm) 程度伸びるのですから、意外と大きい数字で、これが3次元的に変化すれば、品物全体に大きな内部の力(応力)が加わって、温度とともに伸び縮みしますが、最終的にどのような変形としてでてくるのかは予想は難しいのです。
変形する力は非常に大きな力で、それが品物の形状を歪めるのですが、弾性変形域を超えて塑性変形してしまえば、品物の変形は残ってしまうことになります。
ただここで、上図の加熱冷却時の寸法変化の図からわかるように、 変態する温度以下の加熱冷却では、ごくゆっくり加熱冷却して品物の各部に温度差がないようにすれば、熱による変形の程度はおさえられる・・・ということが言えます。
冷却速度は、熱処理後の特性(例えば、硬さなど)を考えると、変形のコントロールには利用できそうにないので、冷却中の変形を少なくするには、外力によって変形を抑え込んだり、焼きが入るまでの高温状態でプレスするなどで修正するなどの方法が必要になります。
ただし、熱変形は抑えられるというものの、現実的には、品物全体を温度差がない状態に加熱冷却するのは難しいし、時間的にも制限があるので、「熱処理すれば変形は生じるもの」と考えて、仕上げ加工しろをつけるなどで対策するのが一般的です。
そうはいうものの、この熱処理による変形量を勘案して、最終寸法形状にするための仕上げしろを予想も難しく、一般的には経験に適当な仕上げしろをつけて熱処理をしているのが実情です。
もちろん、熱処理後の矯正(曲がり取り、歪取り)ができなければ、仕上しろ不足で、品物にならない場合も出てきます。
予熱の有効性
熱による変形を少なくする方法の1つは、できるだけゆっくりと加熱することです。
そのために、目的温度まで一気に加熱するのではなく、適当な温度にいったん保持する「段階(階段)加熱」の操作をします。これが「予熱」です。
(予熱の例)
焼入れ性の良い鋼種(例えば、空冷によって硬化する鋼種)では、恒温処理(冷却時に一定温度で品物を保持して各部の温度差を少なくする)をしたり、冷却途中で冷却速度を変化させるなどによって、変形を少なくできる工夫がされる場合もあります。
品物を加熱する際には、「熱」は表面から内部に熱が移動しますので、特に凸部や角部は、凹部や隅部に比べて昇温しやすく、冷却時はその逆になるので、当然、加熱冷却中には、品物各部の温度でが生じて、それが熱変形の原因になります。
このために、大きな品物や形状の不均一な品物の変形を防ぐためには、ゆっくり加熱したり、予熱を段階的に入れることは効果的な方法ですが、反面、これらは、熱処理時間が長くなり、不経済です。
予熱温度
鋼の焼入れにおける予熱温度の第一候補は、730℃付近のA1変態点と呼ばれる温度を基本にして考えます。
その変態点の上下付近の温度で品物を保持して、均一な温度にすることで、熱膨張に伴う変形を軽減しようという考え方です。
もちろん、変態点以下と変態点以上のそれぞれで温度を保持したりして、保持する温度段階を多くするほうがいいのですが、時間が長くかかってしまうので、実際には、750℃~800℃程度での予熱温度を採用することが多いようです。
これを「1段の予熱」といいます。
ただ、予熱を多段階にすることで、イメージ的には変形を少なくできるはずですが、加熱中の自重による変形や炉の温度不均一など、様々な要素が入り交じるために、品物の大きさや炉の特性なでを勘案しながら、経験的に加熱パターンを決めている場合がほとんどです。
変態点を通過する時の鋼の状態
A1変態点は、 加熱時でいうと、鋼の結晶構造が体心立方晶から面心立方晶のオーステナイトという状態になる温度で、その温度は、昇温速度が速いと平衡状態図などに書かれた温度よりも高温側に移行します。
例えば、カタログなどに書かれた加熱時の変態温度が750℃の鋼であれば、ソルトバスなどを用いて、一気に焼入れ温度まで上昇させると、変態点温度は800℃以上の温度になります。
そのために、1段だけの予熱温度を考える場合は、変態点を超えると焼入れ温度になるので、変態点以下の700℃などにするのが効果的なように思うのですが、品物の形状が複雑であったり、大きかったりすると、各部の温度差が加わって、変態点にかかる時点のタイミングが異なってきますので、この温度よりも高い温度が採用されていることが多いようで、結局、予熱温度は、経験的に決められているようです。
作業中の変形対策
加熱中の鋼は、高温になるにつれて軟らかくなり、品物の持っている強度(硬さや引張強さなど)が低くなっていき、応力が解放されやすくなります。
このために、加熱中に変形を生じるような負荷を与えないようにするのも変形を押さえるためには有効です。
変形を少なくするためには、外力や自重で変形しないように、加熱炉にセットする時には品物をまっすぐにたてて保持したり、吊り下げたり、変形を拘束したり、 当てがねをしたり、炉などへの装入のしかたを工夫する・・・などの、変形の予防・矯正の処置がとられます。
その他に、 極端に熱源に近づけないことなどの操業中の配慮が必要です。
焼入れ時の変態による変形
変態時の変形も重要です。
加熱中にオーステナイトになるときに変態によって体積が減少し、品物の焼入れ冷却時には、オーステナイトが焼入れによってマルテンサイトに変化するときに体積が膨張します。
さらに、温度勾配が大きいと、 熱による変形が加わりますので、断面形状が非対称のものでは、さらに変形動向は複雑になります。
変態による変形の対策
焼入れによって生じるマルテンサイトは、温度の降下とともにその量を増しますので、Ms点に近い温度域において、 各部位を均一保ちながら冷却することが変形を少なくする要素の一つと言えます。
焼入れ時の冷却過程は、(書籍などでは)単純に「連続冷却」を前提にして説明されることが多いのですが、現実的には品物内外は不均一な温度になっています。
このために、熱処理変形の対策としては、特に、 Ms点付近(焼きが入り始める温度付近)の温度降下を調節して変形を少なくする操作をします。
この方法には、例えば、油冷などでは冷却途中で引き揚げて冷却速度を調節したり、冷却剤の温度を調節したり、冷却性能を調節した冷却剤を使う・・・などの方法があります。
変形は、焼入れによって生成したマルテンサイトと、変態しない残留オーステナイトの割合にも関係します。
高合金鋼では、通常の焼入れでも残留オーステナイトが多いために、焼入れ温度を上げすぎないことや、確実に焼戻しをすることなどの、残留オーステナイトを増やさないことも変形を少なくさせる要素の一つです。
一般的な対策では、マルクエンチ(ソルトバスなどの恒温槽を用いて、マルテンサイト変態温度直上で品物の温度を均一にしてから焼入れ変態させる方法)などを行うことが有効と書かれている場合もありますが、鋼種や品物の状態によって条件が変わるために、それをすることで、かえって、変形が増加することもあります。
変形に及ぼす要因は非常に広範であるために、変形の予測や対策は簡単ではないので、頭で考えるようにはうまく行かない場合が多く、一回きりの品物に対しては、経験や勘で考える場合も少なくありません。
変形を矯正する
熱処理中の変形が出ないようにすることはもちろん、矯正することも考えないといけません。
鋼が柔らかい状態であれば、外力を加えて修正したり、変形しないように拘束することは可能です。
「プレスクエンチ」「金型焼入れ」などと呼ばれる方法は、金型(治具)で品物を拘束して焼入れすることで変形をおさえる方法で、大きな治具を用いて品物を挟み込んで焼入れ冷却します。
このように、変形は焼入れ過程で発生しやすいので、曲りの方向を予測してあらかじめ逆方向に変形させたものを焼入れしたり、焼入れ硬化する温度の手前で、外力を加えて矯正する方法などが実施されていますが、形状の異なる小ロット品の場合は、対応できない場合が多々あります。
さらに、変形の状態(方向や量)が予測できにくいこともあって、矯正作業は経験と熟練を要します。
常温で矯正するこのが危険であれば、熱を加えて矯正しますが、費用の問題があるだけでなく、確実に矯正できるかどうかも、やってみないとわからないということも多く、熱処理変形は、頭の痛い問題です。
ここで、ページを替えて、「焼割れ」や焼戻し時の変形については、次のページで説明しています。
↑このページの上へR2.4 CSS変更 R2.8写真の整合化 最終確認R6.4月