このページでは、工具鋼SLDの技術資料で、図表などの見方を説明しています。
プロテリアル(旧:日立金属) SLD のカタログデータの見方
プロテリアル(旧:日立金属)のSLDは、SKD11の相当品として、冷間工具鋼などの、いろいろな用途に幅広く使用されています。 入手しやすく、価格もリーズナブルなことから、SKLD11相当品は、各製鋼メーカーからも販売されており、 色々なサイズが流通しており、使いやすい鋼種の一つです。
JIS鋼種のSKD11相当品は、大同特殊鋼のDC11 プロテリアル(旧:日立金属)のSLD 山陽特殊製鋼のQC11 日本高周波鋼業のKD11 ・・・ というように、特殊鋼メーカーでは各社ブランド名で販売されて流通しています。
品質的には、各社とも、それぞれに特徴をPRしていますが、いずれも、これらの品質はJIS品質を超えた高品質になっていますので、SKD11と言わずに、それぞれのメーカー名で呼称するのが適当です。
このSKD11の 1.5%C-12%Cr の成分系は、世界各国でも標準的な鋼種で、アメリカのAISI規格の「D2」は有名で、冷間工具鋼の代表的な鋼種です。
私自身も、SLDは50年以上にわたって使ってきましたし、プロテリアル(旧:日立金属)さんが公表しているSLD関連の技術資料やデータも豊富ですので、ここでは、SLDのデータでSKD11の特性データやグラフの見方考え方を簡単に紹介します。
焼入れ特性
このグラフは、焼入れ温度と硬さの関係が示されています。
SLDに限らず、すべての焼入れして硬化する鋼種では、このグラフのように焼入れ温度を変えて硬さを測定すると、上記のお椀を伏せたような形になり、最高硬さの出る、少し低温側の温度を「標準の焼入れ温度」として考えます。
カタログには、空冷(A.C)で、1000-1050℃が適正焼入れ温度と表示されています。
このグラフを見ると、約1025℃で最高硬さが出ていますので、1020-1030℃程度が焼入れの際の加熱温度ということになります。
私は、できるだけ焼入れ温度を高くしない方がいい・・・という考え方をしており、最高硬さを求めないのなら、できれば低めの1000-1020℃を推奨します。 (最高硬さが必要な場合は、この図の温度で焼入れして、さらに低い温度の焼戻しになるのですが、62HRC以上の硬さはオススメしません)
下の顕微鏡写真は、焼入れ温度に対する組織が紹介されています。
オーステナイト化(焼入れのための昇温)において、適正温度範囲を低温側にはずれると、 合金元素の溶け込み不足になって、硬さが十分に出なくなります。 高温側にはずれると、結晶粒界がはっきりしてきて、結晶粒も大きくなり、(組織ではわかりませんが) 残留オーステナイトが増えて、やはり硬さが低下傾向になります。
そのために、適正焼入れ温度で加熱するようにします。
カタログでは示されていませんが、一般的に、焼入れ温度の過度の上昇によって衝撃値は減少しますから、必要以上に焼入れ温度を上げることは避けるべきでしょう。
焼入れ温度の選定については、「じん性が必要な場合は適正温度内の低目の温度を採用し、耐摩耗性が必要な場合には高めの温度を採用する・・・」ということで説明されることが多いのですが、必要な硬さが確保できるのであれば、あえて高めの温度を取る必要はないと考えておくのがいいでしょう。
もちろん、適正焼入れ温度範囲を超えないようにしないといけません。
焼入れ温度が高い場合は、残留オーステナイトが増えて、 焼入れ硬さの低下が起きますし、製品になった時に、経年変化による変形や使用中での問題が生じる可能性も出てきます。 こては、下でも説明しています。
もちろん、機械的性質に対する影響は、焼入れ温度だけでなく、加熱時間と温度による、結晶粒の成長や、冷却方法による組織の違い・・・なども関係します。
(注)これらの写真や図表は、カタログの写真をコピーして加工していますので、倍率等は不詳です。 また、このページの図表等は、 プロテリアル(旧:日立金属)カタログHY-86-cのものを説明のために使用させていただいていますので、きれいな図が必要なら、プロテリアル(旧:日立金属)のHPなどを参照ください。転載しないようにお願いします。
焼戻し硬さ曲線
SLDの焼入れ温度を変えて、空冷で焼き入れた後、各温度で焼戻しした硬さが示されています。 これは「熱処理曲線」「焼戻し硬さ曲線』などと呼ばれます。
500℃付近で2次硬化と呼ばれる硬さの上昇がみられます。
ただ、SLDでは高温の焼戻しでは58HRC程度の硬さ以上はでませんので、硬さが高くなければ、用途が限られることもあるので、SLDを高温焼戻しして使用する用途は少ないでしょう。
また、これらの熱処理曲線の作成に試験片は、15mm丸以下の小さなものなので、実際の大きな製品では、同じ硬さや硬さ推移にならないこともあります。
200℃前後の焼戻しで高い硬さで使う
冷間用の工具の用途では、多くの場合には、60HRC以上の高い硬さで使用する場合がほとんどですので、通常は、200℃前後の焼戻しで使用します。
もちろん、57HRC以下の硬さにしたい場合は、500℃以上の焼戻しをすることになりますが、高温の焼戻しは、少なくとも2回の焼戻しが必要です。(→工具鋼の焼戻しを参考に)
前者の200℃程度の焼戻しを「低温焼戻し」、後者を「高温焼戻し」と区別して呼ぶ場合があります。
残留オーステナイト
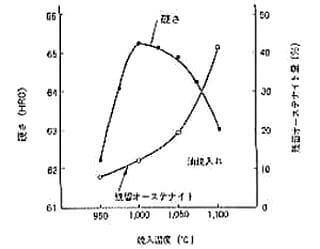
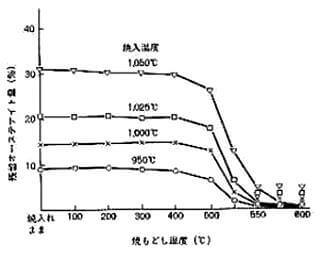
残留オーステナイトとは、鋼を焼入れした際に、常温になっても硬い焼入れ組織にならずに、高温にあったときの組織の名残が残ってしまったものです。
この残留オーステナイトは、いい点よりも悪い点が多いので、できれば、これをなくしたいのですが、残念ながら、成分的なことなので、どうしようもありません。(残留オーステナイトについては、こちらの「焼戻し」の項で説明しています)
上図左は、焼入れ温度と残留オーステナイト量と焼入れ硬さの関係を示したもので、上右図は、焼入れ温度を変えた試料を焼き戻ししたときの残留オーステナイト量の変化を示しています。
いずれも、適正温度範囲を超えて高い温度で焼入れすると、急激に残留オーステナイトが増えていることがわかります。
適正焼入れ温度で加熱しても、この残留オーステナイトがなくならないのですが、ともかく、焼入れ温度を守ることが重要です。
SKD11(SLD)はMs点(焼入れして硬化するマルテンサイトが生じ始める温度)が180℃程度と低く、Mf点(焼入れ硬化が完了する温度)が常温近くにあるので、残留オーステナイトが多い鋼種で、通常の熱処理作業では、品物が大きいと、われ防止のために、十分に低い温度まで冷却しないので、さらに残留オーステナイトが多くなってしまいます。
残留オーステナイトは400℃以上の焼戻しによって分解を始め、(他のダイス鋼の鋼種でもほぼ同様で)550℃程度以上でほとんど消失することが確認されていますが、このような焼戻し温度で硬さを決めることも少ないので、低温焼戻しをしたものでは、残留オーステナイトを残したまま使用しています。
この残留オーステナイトの多い少ないや存在の可否については、色々な考え方があります。
長所としては、その軟らかさがショックアブソーバーとなって、じん性値を高める効果があるとされています。
反対に、残留オーステナイトは不安定な組織で、経年変化し、割れや変形の原因になっている・・・などの短所があります。 さらに、10%以上が残留するのは好ましくないという意見もあります。
そうなると、少なくても、残留オーステナイトを多くするような熱処理は避けたほうがいいことには間違いなさそうです。
焼入れ温度は高くしない
焼入れ温度については、焼入れ温度が高くなると、オーステナイト結晶粒が大きくなって、最終的なじん性値が低くなることがわかっていますし、残留オーステナイトが増えるのであれば、適正温度範囲内であっても、低めの温度で焼き入れるのが無難です。
熱処理の基本的な考え方では、「焼入れ温度は高くしない」「焼入れ保持時間は必要以上に長くしない」「冷却速度を遅くしない」・・・などがあるのですが、高い硬さが欲しい場合は、どうしても、高めの温度にしたり、確実に温度を上げて焼入れしたい・・・と考えてしまいがちです。注意しましょう。
機械的性質
SLDのカタログの多くには、焼戻し温度に対する機械的性質について、引張特性、耐圧縮性、じん性、疲労強度、摩耗特性などが示されます。
また、物理的性質として、ヤング率、 熱膨張係数などの変化が示されている場合があります。
一般的に言って、引張強さ、圧縮強さは「硬さ」との相関があります。 硬さが高くなると「強さ」が高くなります。
引張強さは、焼戻し脆性などの特殊な問題点は別にして、多くの鋼種では、 硬さ換算表に掲載された近似値からその特性を考えればいいのですが、むやみに高い硬さにすると、引張強さが低下するので、冷間で使用する場合は、200-250℃程度の適当な温度で焼戻しして使用するのがよい・・・ということを知っておいてください。
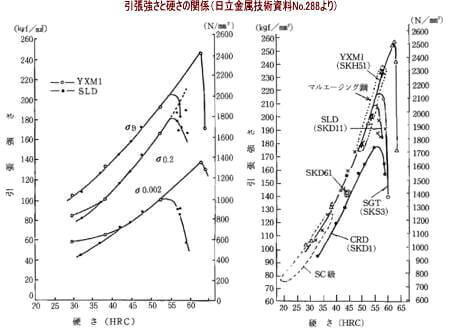
次に、じん性については、焼戻しして使用することの重要性に注目します。
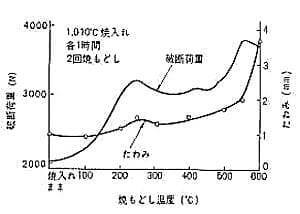
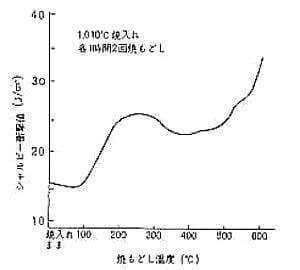
上左は5mm丸x50mm長さの試験片による抗折試験結果で、上右は10Rシャルピー衝撃試験結果です。
ここでも、焼戻し温度が200-250℃程度の焼戻しをすることで、急激にじん性(破断荷重やシャルピー値)が増加しています。
これは、上で書いたのと同様に、最高硬さで使うのではなく、200℃程度の焼戻しをして、少し硬さが下がっても、その状態が優れた状態であることがわかります。
高温で焼戻しすると、じん性が高くなっていきますが、硬さが低くなってしまので、工具としては使えなくなってしまうかもしれません。 このグラフは、高温に焼もどしするほうがいいということを示しているのではありませんので、注意してください。
半冷時間
基本的な指標ではありませんが、プロテリアル(旧:日立金属)は、非常に大きな品物を熱処理した場合の表面硬さやその中心部の硬さを推定する方法として、半冷時間による硬さが示されています。
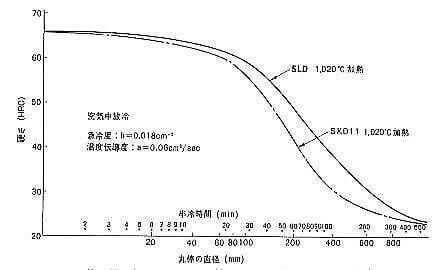
焼入れしたときに、焼入れ温度と室温の中間温度になるまでの冷却時間を「半冷時間」としていて、冷却が遅くなることによる、硬さがどうなるのかが示されています。
たとえばこの図で、焼入れ温度が1020℃で室温が30℃とすると、半冷温度は、(1020+30)÷2=525℃ で、上の図では、その温度までを、30分以内で冷却すると、その表面硬さは60HRC以上を確保できる・・・というようなことを、この図で読み取れるようになっています。
その他の半冷曲線もカタログなどに紹介されていまて、半冷曲線の中には、たとえば、中心部の硬さの低下度合いを推定することができるデータもあります。
このような半冷曲線が、熱間工具鋼など他鋼種についても作成されていますので、鋼種間の焼入れ性の違いも見ることができるようになっています。
摩耗試験
これは、大越式迅速摩耗試験機でのテスト結果の1例です。(摩耗試験・耐摩耗性については、こちらも参考に)
大越式摩耗試験は、試験が、数分間という、比較的短時間で行えるので、よく使われる摩耗試験方法です。
この試験では、SCM415のリングを回転させて、400mの摩擦距離で摩擦させて、焼入焼戻しをしたSLDを66.7Nの力で押し付けたときの摩耗量を、6つの速度の場合で比摩耗量として示されています。
この試験方法では、0.2m/s以下の低速の摩擦では、どのような鋼もほとんど摩耗量の差は見れず、2m/s以上の高速になると、発熱が大きくなるので、耐熱要素の強い鋼種や熱処理条件が有利になるので、示される多くの場合は、上のような多点のデータではなく、下の図のように、1m/s前後の摩擦速度の場合だけを示して、その比摩耗量を表示されることが多いようです。
下図は、系統の違った鋼種を一覧にしているので、余計に読み取りにくいのですが、ここでは、硬さ、焼戻し温度、成分の影響が読み取れます。
しかし、通常はこのような多鋼種・多条件の試験をする場合は少なく、鋼種間の違いを見る場合などでは、例えば、硬さを同一にしたときや、熱処理条件の違いによって、摩耗量がどうなるのか・・・を見るような試験の仕方をします。
この表は、鋼種間の違いを見るために作られているものなので、硬さが違ったり、焼戻し温度が大きく違うので、結果に見方には注意が必要です。
0.78m/sで400m摩擦させると、400/0.78 で、約9分で試験をするので、非常に速いのですが、試験片の加工や摩擦痕から摩耗量を算出したりするのも熟練がいりますので、誰もが簡単にできるというものではありません。
熱処理変寸
熱処理での変寸は、組織変化に伴う寸法変化を言います。
下図は、圧延方向に対して試料の取り方を替えた場合の、焼戻しに伴う寸法変化を示しています。
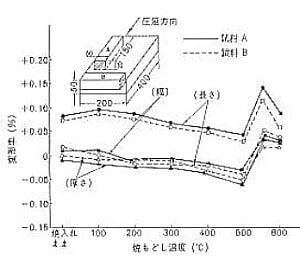
SKD11(SLD)は、500℃以上の焼戻しで2次硬さと呼ばれる再硬化現象が見られるので、大きな寸法変化が見られます。 また、材料の取り方の方向によって、変寸する値が異なっていることに注目しましょう。
これは1つの例で、実際には、鋼材ごとにこの変寸率は異なります。 つまり、材料の履歴(鋼塊寸法や圧延の圧下率、製品の寸法・・・)などで、熱処理後の変寸率は、この図と同じにはなりません。
上の試料Aのように圧延方向に沿った場合でも、私の経験でも、長さ方向でその値は、+0から+2%程度の幅でばらつきがあるのが実情ですが、変寸の傾向や温度変化については、このグラフは参考になります。
変形は3次元的に生じますので、材料どりの方向が違えば、品物の変形の状態が変わってくるということです。
品物が大きいと、小さな変寸は大きな変形になります
これは小さい品物の場合はそんなに問題ないのですが、1mの0.1%は1mm、3mの品物では、3mmも伸びてしまいますし、その数字が品物によってバラバラだというのは、どうしようもありません。
これは、実測値の1例で、(こちらに変寸についての記事があります) 熱処理前の購入した材料素材の状態が影響するので、熱処理の工程で変形をコントロールできる範囲や量は限られているので、変寸・変形は非常に厄介なものといえます。
ここでは詳しく説明しませんが、この対策として、通常は、変寸を予測して、穴ピッチを修正しておいたり、仕上代を余分に付けておく方法をするのですが、完璧を期す場合は、同じ材料を用いて、同断面形状で小さい品物を予備に熱処理をして、その寸法変化を見て、寸法修正をする場合もあります。
この、材料に伴う寸法変寸は、何十年にわたって鋼材を使っていても解消されないもので、さらに、ユーザーだけではどうにもならない、困った問題です。
ただ、上のようなグラフがあれば、鋼種が同じであれば、数値の多少はあるものの、焼戻し温度による推移傾向は変わらないので、寸法修正はどうするのかや、焼戻し温度を上げるとどのような変寸や変形が推移するのか・・・などが少しは推定できるので、非常に役に立つデータです。
↑このページの上へ最終確認R6.4月