鋼の表面熱処理について
一般的に鋼の表面に施される「表面処理」と呼ばれる加工があります。
鋼の表面処理の種類には、「メッキ」「溶射」「ライニング」「コーティング」「塗装・転写・スタンプ」 「化成処理」「表面硬化」「チッカ処理」 その他 ・・・ などがありますが、鋼の熱処理に関するJISには、鋼の表面熱処理で、炎焼入れ、窒化、浸炭 などが規定されていますので、この簡単な説明と、トラブルが起きやすい注意点などを紹介します。
浸炭焼入れや火炎焼入れは、焼入れで、硬化層はmm単位ですが、窒化は0.01mm単位です。
さらに近年、窒化処理で、いろいろな特徴のある窒化処理が開発されていて、処理各社がオリジナルな処理(加工)名をつけているのですが、特徴が多岐にわたってわかりにくくなっているようです。
表面処理をすれば、価格に見合う効果があるというものではないし、熱を加えるのですから、それについても知っておく必要があり、処理コストもまちまちです。
普通の熱処理では考えられない効果もあり、うまく適合すれば、数倍の寿命になる場合もあるので、耐摩耗性の向上や寿命延長の効果の高いものを探してみるのもいいでしょう。
詳細は、ここでは取り上げませんが、一般的で熱処理と関係深いJISに規定されている「熱を加える表面処理」の内容や問題点、対策などについて説明します。
鋼の表面を硬くする表面熱処理
JISには、「火炎焼入れ」「高周波焼入れ」「浸炭焼入れ」の表面硬化処理が規定されています。
通常は、これらの処理は、専門の業者さんに委託することが多いのですが、その場合にも、前熱処理や後熱処理などが関係する場合があるので、大きな失敗をしないように、簡単な知識を持っておいたほうがいいでしょう。
火炎焼入れ(炎焼入れ)
「フレームハード、フレームハードニング」などともよばれます。
加熱をバーナーなどで行う熱処理法で、プロパンガスやアセチレンなどと酸素の混合ガスを用いるものが多く、鋼種の焼入れに適した温度(800-1050℃程度)に加熱して焼入れするのですが、一つずつ手作業での作業がほとんどで、温度調節や鋼種の焼入れ性に応じた冷却、焼入れ部分の硬さや硬化深さのコントロールなども「職人技」のところもあって、熟練がいります。
さらに、焼入れ部分の面積が増えると、予熱して作業することもあって、非常に熱い作業をしなければならない・・・などから、どちらかというと、少量の品物を簡易的に焼入れする方法と考えてもいいものです。
焼入れした状態の品質は、個人技量によるところが多いので、少量の加工金型などで行う場合が多いのですが、近年、「火炎焼入れ鋼」と呼ばれる鋼種が販売されて、かなり焼入れ作業が簡単にできるようになっています。
火炎焼入れ鋼について
大同特殊鋼「GO4」、プロテリアル(旧:日立金属)「HMD5・HMD1」、日本高周波鋼業「FH5」、山陽特殊製鋼「QF3」、愛知製鋼「SX105V・SX4」、ウッデホルム「FERNO」などの鋼種が「火炎焼入れ鋼」として、各社から販売されています。
各社ともに、扱い量(製造量)はそんなに多くはありません。
これらの鋼種は、空冷(加熱後の放冷)によって硬化する鋼種で、ガスバーナーで鋼材の一部を加熱して、放冷する際に母材に熱を奪われて、空冷で硬化するように設計されている鋼種です。
SKD11などのダイス鋼に比べて安価なこともあって、火炎焼入れで焼入れするのではなく、通常の全体焼入焼戻しをして、機械部品を製作する場合も多いようです。
焼入れ方法は、バーナーで加熱色(→こちらを参考に)を見ながら、順送りに切刃部分を加熱するだけで、バーナーの炎が離れると、金型に熱を取られて冷却され、焼入れ硬化します。(空冷で焼入れできる、空気焼入れ鋼です)
焼戻しは必ず必要で、これを、バーナーで炙るだけで済ます場合もありますが、できればしっかりと焼戻しするほうがベターです。 焼戻しは、200℃程度に焼入れ部分を加熱して焼戻しします。
焼戻し用の加熱炉がない場合でも、小さい金型であれば、天ぷら油を160-180℃に加熱した中に金型を入れて、1時間程度加熱することでも、しっかりと焼戻しができます。
火炎焼入れ鋼は、目視温度でバーナー加熱できるように、加熱温度幅が広く、また、刃先などの小さな部分であれば、空冷で焼きが入る材料ですから、一般的に形材などに使用される鋼種のように、「水冷」「油冷」などで硬化させる必要がありません。
しかし、高合金のダイス鋼(たとえばSKD11など)に比べると、耐摩耗性やじん性は低いので、軽負荷の小ロット用の金型用向けの材料といえます。
ガスバーナーを用いて手動で作業する場合は、通常の鋼種では、加熱温度が不安定になって、均一な硬さが得られにくいのは当然ですが、これらの鋼種は、バーナー加熱に対応するように、焼入れ温度の幅が100℃くらいに違ってもいいように成分設計されており、200℃程度の低温焼戻しで60HRC以上の硬さになります。
軽負荷の金型やトリム型(抜型)の切刃部分先端の焼入れ硬化させる金型などで使いやすいように考えられているようです。
もちろん、焼入れによる変形はします。
しかし、一部分の加熱なので、全体加熱する場合に比べて、焼入れ後の変形は少ないのですが、焼入れすればその部分の寸法変化はあるので、全く変形しない・・・ということではありません。
それもあって、単純な形状の角部や幅広い面の硬さが必要な場合には、火炎焼入れをしないで、普通に全体加熱する焼入焼戻しをするほうが変形が少なことも多く、火炎焼入れ鋼といえども、通常の鋼と同じように全体焼入れして用いられることも多いようです。
高周波焼入れ
これは、高周波電流を加えて、電磁誘導による渦電流の表皮効果で表面部分だけを短時間に加熱して焼入れする熱処理方法です。
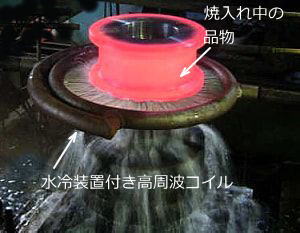
高周波焼入れの特徴は、例えば ①φ60程度以上のS45C の丸棒でも、表面硬さが60HRC程度の硬さが出ること、 ②低合金鋼でも、炭素量に応じた高い硬さが得られること、 ③軸内部の硬さが軟らかいために折損などに強いこと、 ④表面の圧縮応力が有効に作用して疲労強度に優れること・・・などがあって、特に軸類などの棒状の製品の円筒面の焼入れに適しています。
軸の外周部に限らず、平面の一部を硬化させることもできるので、非常にポピュラーな熱処理法です。
周波数によって硬化深度は変わります
高周波電流は、その周波数によって、硬化できる深さが変化する・・・という特徴があります。周波数が高くなると、焼入れ深さは浅くなります。
近年はインバーター技術や電子技術も進んでおり、硬化深さについては、周波数などの条件を変えることでそれができるようになっています。
特に硬化させたい深度がほしい場合には、大電流で、低い周波数帯の高周波装置を用います。これは「高周波」ではなく、あえて「中周波焼入れ」と呼ぶ場合もあります。
全硬化層深さは、周波数が100KHz程度で2mm前後、10KHz程度で3mm前後、 1KHz程度で7mm程度を目安にするといいでしょう。(全硬化層については、思い違いが多いので、この後ろの記事を参考にしてください)
焼入れ性の良い高価な材質は不向きです
このような誘導加熱では、焼入れ性のいい高合金鋼は、焼入れ硬さが充分に高くならない場合もあるので、むしろ、安価な材料を用いるほうが無難です。
SC材やクロモリ鋼などの機械構造用鋼でも高い硬さが得られることが高周波焼入れの特徴といえます。
加熱後の冷却には、ソリブルと呼ばれる、水溶性のポリマー溶液などが用いられます。 これは、一般の熱処理で言えば、水冷と油冷の中間の冷却速度にしている場合が多いのですが、高周波による、非常に短時間の焼入れ処理で、充分に高い硬さになります。 それもあって、熱処理対象の多くは、構造用炭素鋼や低合金鋼が主流になります。
S45C(60HRC以上)やSCM435(58HRC以上)、SUJ2(62HRC以上)と、比較的に、低合金鋼では、炭素量に見合った硬さ(→こちらを参考)が出ますが、逆に、合金量が多い SKT材、SKD材などでは炭素量が0.5%以上あっても、残留オーステナイトの影響で、57HRC以上の硬さが出にくくなります。(処理条件によって変わりますが、このように覚えておくといいでしょう)
強さ+耐摩耗性には、調質+高周波焼入れ
高周波焼入れで、表面の硬さを上げることができますが、軸などで使用する、全体強度が必要なものは、高周波焼入れをする前に全体を「調質(焼入焼戻し)」しておいてから表面を高周波焼入れをします。
この場合には、必要な芯部の強度に応じて、S45Cなどの炭素鋼の他に、合金鋼(SCr材やSCM材など)が使用されます。
高周波焼入れの硬さは、低合金鋼であれば、0.4%C以上であれば、80HS(59HRC)程度の硬さが得られます。
高周波焼入れで問題が起きやすいこと
高周波焼入れの特徴や制約について知っておくと、トラブルを未然に防ぐことができます。
硬さのムラはある程度出るのはしかたがない
丸棒の外形などを焼入れる場合の高周波焼入れは、品物を回転させながら加熱部分を移動して焼入れするという方法をとるので、比較的に、表面硬さが一定になるものの、コイルの間で硬さが低くなる傾向があり、均一な硬さにはなっていません。
これは、2重焼入れ(同じ部分を加熱すること)を避けるために、送り幅の継ぎ目で若干の表面硬さむらが生じるのですが、これは仕方がないことです。
極端に言えば、縞々に硬化しているのですが、軸の場合は面で接するので、これでも問題が生じることは少ないといえます。
この硬さムラを小さくするために、送りピッチを小さくしすぎると、焼割れが生じやすいなどの問題も出やすいので、高周波焼入れによる微小硬さムラはある程度避けられないもの・・・と考えておくといいでしょう。(高周波焼入れでは全面均一な硬さにならないことを知っておきましょう)
円筒の端面まで硬さが必要な場合は注意
通常の作業では、端面割れを防ぐために、品物の最端部を加熱しないようにするのが通例で、そのために、端面外周の硬さは低い状態です。
もしも、端面から充分高い硬さが必要な場合は、予め長く仕上げておいて、高周波焼入れをしたあとで、焼きの入っていない端面を切り落とす・・・などの方法を取ります。
このように、通常の高周波焼入れでは、両端部の硬さが保証されていないのですが、これが不具合になる例も経験しています。 問題がでないように、熱処理前に、図面や仕様を提示して、事前に打ち合わせておくとよいでしょう。
平面部分の高周波焼入れも可能です
高周波加熱による、円筒の外周部以外の、平面の部分の焼入れも可能です。
しかしこの場合も、コイルまたは品物を移動させるために、硬さむらが生じやすく、全面を均一にしたり、硬さ保証を要求するのも難しいもの・・・と考えておいた方がいいでしょう。
また、専用コイルが必要になる場合には、その製作のための負担金額についても確認しておく必要があります。
焼入れ用のコイルは、熱処理費用よりも高額の場合があるので、事前打ち合わせが必要です。
その他、歯車状の品物などで、全体を一気に焼入れすることを「一発焼入れ」と言いますが、このための、製品個々の形状にあうコイルを作成するのは非常に費用がかかるので、加工業者さんの手持ちがない場合は、その費用は別に請求される場合も多いので、設計や見積もり段階で、それらも考慮して事前に打ち合わせしておくのが無難です。
浸炭焼入焼戻し
浸炭の方法には、固体浸炭、ガス浸炭、液体浸炭、真空浸炭、プラズマ浸炭などの種類があります。
浸炭とは、低炭素鋼や低合金鋼などの表面に炭素を浸透させて、焼入れしたときの表面硬さを得やすくする処理を言います。
浸炭深さを深くするためには、特に時間的な要素が大きく、それが納期や費用に関係することになります。
設備や内容によって、「①浸炭+②焼入れ+③焼戻し」の工程を順次に分けて行う場合と、「浸炭~焼入れ~焼戻し」 までを一気に同一炉内で行う場合があります。
昭和年代は、「固形浸炭」という、黒炭を浸炭剤に用いる方法が行われていましたが、近年の、ガスを用いた「ガス浸炭」では、後者が主流です。
浸炭熱処理は、表面を特に硬化したいために行うもので、焼入れ操作としては、「全体焼入れ」と同様に、品物全体を油などの冷却槽に入れて冷却します。
浸炭焼入焼戻しを行うと、品物の全体が焼入れ状態になるので、中心部が軟らかいけれども「ねば硬く」、表面は浸炭により硬さが高い状態になります。
一般的には、低炭素の「肌焼き鋼」と呼ばれる鋼種が多く使用され、浸炭時の焼入れで、その部分も、同時に焼入れされて、強靭な状態になります。
表面熱処理を行う場合の注意点
最近広範囲に行われてきた表面処理には、①焼入れ温度に近い高温で、焼入れと同時に処理されるもの(CVD処理) ②焼入れとは別に、500℃前後あるいは、 それ以下の温度で処理される表面改質(窒化やPVD処理、その他の被膜処理)などがあります。
CVDやPVDによって表面に得られる処理層は、ミクロン単位の、非常に薄い層です。
それもあって、加熱することによる母材の硬さ低下や、処理することによる寸法変化や品物の変形変寸による問題が起きないように、熱処理で対処できる場合は、事前に対策しておかなければなりません。
①の代表はCVD処理で、表面処理の温度が高いので、焼入れ温度と処理温度が同じような鋼種を選ぶ必要がありますし、焼入れを兼ねるので、変形と、焼入焼戻し後の寸法や寸法公差に収まるかどうか・・・などを検討しておきましょう。
処理層の厚さが薄い処理は、最終に研磨による修正はできないので、事前の検討が必須です。
また、 ②は、窒化関連の処理(軟窒化、炭窒化、複合ガス窒化など)の場合で、通常は、仕上(研磨)加工が済んだ、熱処理済みの品物に表面処理します。
多くの窒化処理は520~580℃の温度域で処理されるので、基本的には、処理温度以上の焼戻しをしておいて、仕上げ研磨をして、その後に表面処理をする工程になります。
熱処理の焼戻し温度を越えて表面熱処理をすると、焼戻し温度を上げたときと同じように、組織変化・硬さ変化・寸法変化・・・を生じますが、多くの場合は、処理層が薄いので、最終の仕上げ研磨はしません。
また、単一の表面処理だけをする以外に、①と②を複合したものや、単一の化合物層ではなくて、いろいろな化合物層を重複させて品物の表面につける・・・などの表面処理法が開発されて実施されていますが、いずれの処理でも、加工前に処理業者と打ち合わせをして、鋼種品物の加工工程と品物の引き渡し状態、前熱処理、表面処理前の寸法及び寸法公差、表面処理後の処置等・・・について協議しておく必要があります。
表面処理を受託する各社では、その表面処理による効果や特徴をPRしていますので、それらをWEBのHPなどで調べて検討し、その上で処理業者に相談するようにしましょう。
どのような処理でも、表面層の性状や硬化層深さなどを温度と時間でコントロールするのですが、その方法のほとんどは非公表の内容が多く、処理を実施する場合は、長所だけを見ないで、処理業者に短所や起きそうな問題点を確認して、問題が起きないような事前の対策をしておくことが大切です。
どのような表面処理に言えるのですが、処理をすれば、ともかく、寿命が伸びるというものではないことも考えておかなければなりません。 使用用途により、適不適があります。
寿命や性能に影響する要素には、材料や硬さだけでなく、表面処理をする前の製品表面の仕上げ程度(表面あらさや高輝度など)が寿命に影響に影響することも多く、表面状態が悪いと、期待した硬化層が得られない・・・などの問題があるなどのその他の要素による異影響もあって、どんな品物でも、表面処理をすると寿命が延びるというものではありません。
多様化する表面処理
近年は、様々な表面処理が開発されています。
たとえば、窒化処理のように、鋼に窒素を拡散させ、 チッ素化合物の高い硬さや表面の変化で耐摩耗性をつける処理にとどまらず、窒化に加えて、その他の特性を持った元素やその化合物を表面に付着させる複合処理、あるいはPVDとよばれる、チタン化合物などの耐摩耗性の高い処理層を得る方法、・・・など、
近年は様々な表面処理が開発されている上に、多様化しています。
窒化やPVD処理では、処理温度が500℃前後のものが多いようですが、表面処理を検討する場合には、その処理温度や仕上がり状態についても同様に 事前に検討しておかなければなりません。
また、温度の影響のないものについては大きな問題はないと考えられますが、電解によるメッキなどをする場合には、処理中の昇温はないものの、 水素脆性の危険性に配慮したベイキング処理(水素飛ばし)などを必要とする場合があります。 もちろん、その温度が焼戻し温度を超えないようにすることが必須であることはいうまでもありません。
最後に、表面熱処理で勘違いや誤解が多い「硬化深さ・硬化深度」について説明します。
JISの「硬化深さ」の落とし穴と注意点
表面熱処理のうち特に利用頻度の多い高周波焼入れにおける硬化深さについて、これを理解していないと、思わぬトラブルになる場合がありますので、説明します。
全体焼入れ焼戻しをする場合でも高周波焼入れをする場合でも、一般的に、熱処理後の硬さは、内部に行くほど低下します。しかし、硬さの測定は、表面硬さしか測定することができません。
特に表面だけの焼入れの場合は、硬化範囲(硬化深さ)が浅い上に、中心部の未硬化部分との境界で、硬さが急変している場合が多いので、後加工(仕上げ加工)の段階で「曲り」が出たり、表面が剥離したり、表面硬さがでない・・・という問題が起こる場合があります。
これを避けるためには、熱処理の特徴や硬化深さの定義を知って、加工業者と充分な打合せが必要です。
ここで「硬化層」について、その定義などを知っておくといいでしょう。
「JIG G 0559 鋼の炎焼入及び高周波焼入硬化層深さ測定方法」に、硬化深さや硬さについて規定されていて、ここには、 「有効硬化層深さ」「全硬化層深さ」「最少表面硬さ」「有効硬化層の限界硬さ」という表現について規定されています。
この言葉の意味を簡単に意訳すると、以下の通りです。
有効硬化深さ:鋼材表面から限界硬さの位置までの距離
全硬化層深さ:焼入れした表面から、焼入れ前の鋼材硬さまでの距離
最少表面硬さ:要求した表面硬さの最低値
たとえば、「60HRC以上」と指定したときは60HRC)
有効硬化層の限界硬さ:最少表面硬さ×0.8(上記の例では48HRC)
ここで、高周波焼入れの場合を例にすると、熱処理を依頼する場合には、「有効深さ」と「硬さ」 という2つの言い方の条件で熱処理仕様を打合せすることが多いのですが、この場合の有効深さは「有効硬化深さ」であり、 硬さは「最少表面硬さ」ということに注意しておく必要があります。
つまり、硬化深さは「限界硬さ」ですから、ほしい硬さを指定しても、0.8倍の硬さのことですから、求めている充分に高い硬さではない・・・ということに注意しておかなければなりません。
例えば、ある丸棒について「表面硬さは60HRC以上で、硬化深さが2mmほしい」と指定した場合に、適正に高周波熱処理をされたものでも、 2mm深さの位置では60HRCは保証されていないということがあるのです。 この点は、十分理解しておいて、注意して打ち合わせする必要があります。
これは一例ですが、この結果、仕上げ加工をしたときに、要求した硬さがでていない・・・ということになるのですが、これはしばしば耳にします。
仕様の打ち合わせは、しっかりしないといけないというよりも、少しわかりにくい表現になっていますので、注意しないといけません。
JISでは、確実に内部硬さを知るのためには、通常検査とは別に、『硬さ推移曲線により測定する』 とあります。 これは、焼入れ断面を切断して、表面から内部への硬さ推移をみる方法ですが、試料を作って測定するまでが大変ですし、余分な検査だとして、追加の費用もかかってくる場合もあるでしょう。
そのために、問題を回避するためには、事前に「仕上げしろ」などを含めて「仕上がったときに、表面硬さを測定して**HRC以上の硬さが欲しい」というように、はっきりと要求を出して、打ち合わせしていくことが重要です。