1.刃物の摩耗
刃物は摩耗によって切れ味が悪くなると再研磨して刃先を立てる必要があります。通常の過程で摩耗が進むと、長持ちしますが、使用方法が適切でなければ急激に摩耗が進みます。
摩耗の要因は、刃物の問題以外にもたくさんあります。
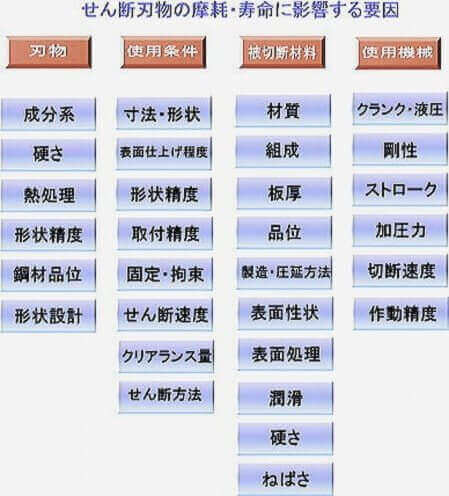
1)刃物材の持つ「宿命」
何度も書いていますが、鉄鋼製の刃物材では「耐摩耗性とじん性」には逆の相関があって、基本的には、どちらかを高くすると、反対の特性は低下します。
いかにマイナス要素を押さえながら、欠けないで長持ちする刃物(刃物材)を作るかがポイントになります。
耐摩耗性を上げるために硬さを上げることや成分系を変えて耐摩耗性の高い鋼種を用いる場合には、当然、じん性値が低くなり、欠けやすくなります。
硬さとじん性の関係はそれが比例関係のように直線的に増減するものではないので、じん性の低下が急激に減少する手前の硬さを狙ったり、最低のじん性を保って硬さを上げる操作を行う場合もしばしばあります。
鉄鋼製の刃物では基本的な相反する性質を無視できませんので、オールマイティーの刃物材を見つけるのは困難ですが、このように、特定の条件用の刃物にするか、 バランスのある刃物にするか・・・の切り分けは必要です。
刃物が鋼板を切る能力があるのは、鋼板の持つ機械的性質(たとえば「硬さ」)に比べて、数段に高い状態に熱処理によって強化されているためです。
この、硬さは、「圧縮強さ・引っ張り強さ」などの「強さ」と相関があって、硬さを高くすると 耐力値も上がって、見かけの弾性変形領域を大きくできますので、 永久変形(塑性変形) しにくくなり、これによって最終的には摩耗しにくくなることで、結果として、寿命が延びる・・・ということになります。
しかし、困ったことに、熱処理によって硬さを極度に高くしようとすると、その相関は50HRC程度の硬さから崩れ始めて、ほとんどの鋼種は、 刃物として使われる硬さ付近では、圧縮強さや引張強さは硬さに比例せずに低下してしまっています。
この耐力限を上昇させる一つの方法では、刃物の合金元素によるマトリックス強化という方法があります。
しかし、やはりこれも同様に、じん性面では、 硬さの上昇とともにじん性値が低下しますので、基本的には、それぞれの鋼種の適正硬さ範囲を超えて使うことは不適当だ・・・といえるでしょう。
このために、熱処理で調整できる範囲を超える場合には、鋼種を変えることで対応することになります。
例えば、圧縮強度(強さ)についていえば、炭素量が高く、炭化物を 生成する合金成分のより多い鋼(たとえば高速度工具鋼のような高合金鋼など)を用いると、高い硬さまでは 硬さと強さの相関が維持されるということになりますし、さらに、炭素Cとともに、クロムCr・モリブデンMo・タングステンWなどによる炭化物の多い鋼種は、 高い硬さ領域まで 圧縮強さ・引張強さは低下しにくくなります。
また、低合金工具鋼よりも 高合金工具鋼が、また、それ以上に炭化物量の多い高速度工具鋼が優れていますので、 その考え方に従って、鋼種を選定することになります。
しかし、合金量の多い「高級鋼」になればすべてに優れるというものではなく、じん性面や価格の面では劣ってくる場合もありますし、 熱処理の焼入れ温度が高くしないといけない・・・などの問題点も考えないといけません。
一般的に、鋼における耐摩耗性は、(1)硬さ (2)炭化物の量 (3)炭化物の硬さ (4)炭化物の大きさ によるとされています。
例えば 薄板切断用刃物の汎用鋼SKD11(および相当品)では、50μmを超える比較的大きな炭化物が組織中にみられますが、それが耐摩耗性に有効になっているために、 それより高価で、硬さが高くて炭化物の多いSKH51などの高速度鋼系の鋼種よりも、低速度の摩擦においては耐摩耗性が優れているという例などもありますので、不必要に高価な鋼種のほうが優れているとはいえず、鋼に熟知するのが長寿命刃物を考える近道といえます。
このように、しばしば、合金量が多い高級鋼になるほど刃物の性能が良い・・・という話を聞くこともありますが、そんなに簡単なものではありません。
たとえば、刃物で切断するものも「鋼」ですので、潤滑などは寿命に大きく効いてきますし、そのほか、性能試験をした時の評価が良くても、 刃物としてそれを使った時に、成績に反映しない場合もたびたびあります。
これは、刃物材の評価方法(試験方法)に乏しいこともありますが、刃物に影響する因子が整理できていない状況なので、まだまだ多くの問題が残っています。
2)摩耗曲線
摩耗の進行は、下記のように推移するとされています。
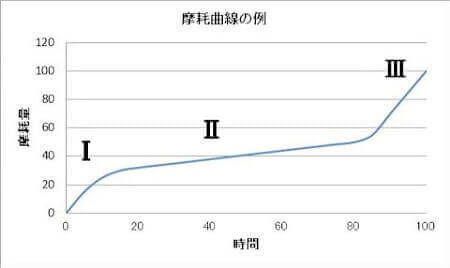
Ⅰの領域は「初期摩耗」と呼ばれ、刃先が大きな圧力に耐えるために、急速に摩耗したり、場合によっては 微小なチッピングを伴って切断力に耐えるように 「刃先の丸み」が形成する過程です。
この過程における対応は重要で、徐々に刃先に負荷をかけることでこの図の曲線を下方に下げる効果があるので、使用期間を大幅に伸ばすことができます。
逆に、急激な負荷を一度に欠けると、刃先には無限大の力が加わるので、その力を分散しようとして、微小チッピングによって接触面積を増やして対応しようとするので、摩耗が急激に進行することになります。
また、別のところでも説明していますが、せん断時には摩擦熱とせん断熱によって熱による焼戻し効果を受けます。このこともあって、刃物の使用初期の「慣らし運転」は重要です。
Ⅱは「定常摩耗域」といわれ、摩耗が緩やかに進行する段階で、この状態では、刃物は安定して使用できます。
Ⅲの領域になると、刃先の丸みの 増加などで抵抗が増し、 発熱などを伴って摩耗が急速に増える状態で「終期摩耗域」と呼ばれます。
摩耗が進行すると、刃物は「修理研磨(研磨修理)」によって研ぎなおして再使用しますが、Ⅲに移行する前に行うことで 有効的に長寿命化が図れます。
このタイミングはもっぱら経験によって判断されていたり、あらかじめせん断量を決めて刃替えや再研磨が行われているのが通例です。
3)摩耗試験の難しさ
摩耗は摩擦とも関係深く、摩耗の形態は、主として、刃物と切断材との凝着摩耗 ですので、これについて対策を考える必要があります。
凝着摩耗は、刃物材と被切断材が摩擦して、熱による刃物材の硬さ低下や凝着による 持ち去りなどによって刃物が摩耗する摩耗形態ですが、刃物材と被切断材の化学成分の 相似性、硬さの差、刃物の耐熱性、潤滑材・・・など、様々な要素が関係するようです。
当社では、試験の簡便さから「大越式迅速摩耗試験機」を使って、押し付け荷重と摩擦速度を変えて摩耗量の評価をする場合が多いのですが、 摩耗量に及ぼす要素要因が非常に多いために、摩耗試験の結果がせん断の条件にあてはめられるかどうかの判断は難しい問題で、 寿命評価は実際の刃物を使用した結果で評価しなければ分からない場合も多いようです。
4)刃物が受ける影響
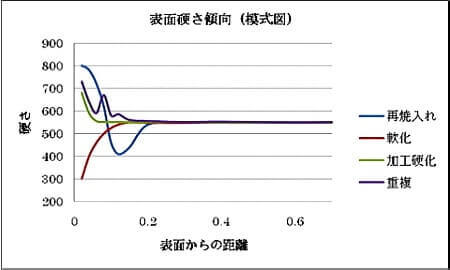
この図は、使用済みの刃物の刃先断面の微小硬さ(模式図)を示したものですが、使用済みの刃先を調べてみると、 上の4つの硬さの傾向に分かれています。 (これは厚板鋼板せん断用の刃物をイメージしたもので、ビッカース硬さ550 ≒ショアー硬さ70程度を想定していますが、 ここではイメージとして傾向だけを見てください)
ここにある、刃先が塑性変形して「加工硬化」が起きている例は、通常の鋼板切断用の刃物では(このような試験方法では)みられることはありませんが、 スクラッププレスシャー刃など1000トン以上の高いせん断力下で使用する刃物に見られる程度です。
ほとんどの製品の鋼板を切る刃物では、塑性変形して加工硬化するよりも、むしろ、せん断時の摩擦熱(または変形時の熱?)の影響を受けて「軟化」 「再焼入れ」の重複によって硬さが変化する場合が多いようです。
つまり、図のように、顕微鏡組織や微小硬さ変化として、焼入れ温度の900℃程度以上に先端温度が上がる例 (「再焼入れ状態」)や700℃程度までの昇温で 焼き戻し効果 によって軟化する例(軟化)、および、 それらが重複した状態などが微小領域で発生していますので、せん断中の熱の影響は非常に大きいといえます。
通常のせん断中にこのような高温になることは考えにくいのですが、刃欠けした事故品の調査をすると、切断材を噛みこんで停止するなどの異常なせん断状況では、熱が放散されずに滞留して組織が変質している例はしばしば観察されます。
せん断の過程では常時、摩擦熱が発生します。 刃物を連続使用していると、手でさわれないほどに熱くなっていることに遭遇しますが、それは、刃先の微小な部分で発熱していることで、切断中に刃物はかなり熱の影響を受けていることが想像できるでしょう。
下図は プレス加工便覧(丸善)その他でも紹介されている図ですが、切断面では、400℃以上となっているのがしめされています。
現状の刃物鋼は、 非常に焼入れ性が良く、空冷によって硬化する鋼種ですので、せん断が繰り返されると、組織変化や硬さ変化が繰り返されて、刃物の割れや欠けの原因になることは、 容易に理解できるでしょう。
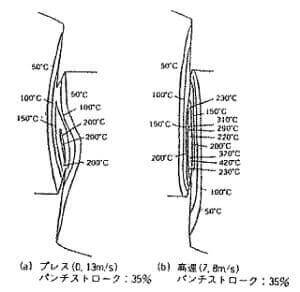
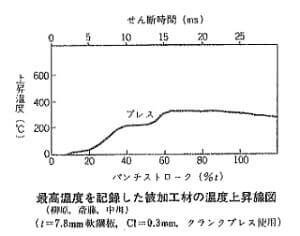
再焼入れされて表面が硬くなっていれば耐摩耗効果が出るようにも思われますが、 この状態は未変態のオーステナイト組織を含む焼入れしたままの 「もろい組織の状態」で、すぐさま、微小チッピング による摩耗につながる可能性も高く、好ましいものではありません。
刃欠け事故があった刃物で調べますと、刃物のコバ面や外周面ではなく、刃物側面にこの再焼入れ現象がみられます。つまり、 切断板との摩擦が多い刃物側面が酷使されている例をよく見ますので、目視では「焼き付き」などが無いように思っても、刃物の極表面は変質していますので、 このような熱影響を受けにくいようにすることが寿命延長のカギといえます。
この発熱の影響を少なくするためには、
①適当な潤滑を考える
②接触距離や接触時間を短くする
③クリアランスなどの設定を変える
④冷やす
・・・などの方法が行われます。
しかし、実情では、せん断面をよくすることが第一と考えられるのが通例で、製品の価値を下げないように「板の表面に 油がつくことを避けるために潤滑油を使いたくない」・・・など
という、刃物にはふさわしくない条件下で使用される場合も多いために、刃物にとっては厳しい状況になっています。
5)被切断材の影響
刃物の寿命に影響する最も大きな要素は被切断材の「硬さ」です。
切断する鋼板の抗張力(引張強さ) が40→60→80→100kg/mm2と上がるにつれて、 当然、刃物への負荷が増します。
この場合の引っ張り強さをビッカース硬さに換算すると、およそ120→150→260→330HVという硬さに対応しますが、 2-3mm切断用の刃物硬さが700HV程度ですので、 概算の引張強さは200kg/?超の程度といえます。
被切断材との硬さ(機械的性質)の差が刃物の生命であり、その硬さの差があることで 刃物が切断に寄与しますので、その差が縮まれば、刃物寿命が低下するのは仕方がありません。
鉄鋼製の刃物鋼では800HV(90HS)程度までの硬さのものが製造されますが、いずれにしても、硬いものを切れば軟鋼を切るのとは違って、寿命が低下するのは避けられません。 といって、それ以上の硬さが出て、その他の性質に優れる鋼製の刃物鋼はなかなか見つからない状況ですので、この場合には「超硬製の刃物」を使ったり、表面処理(窒化やPVD処理など)をして対応する刃物も増えてきています。
せん断材の板厚やその硬さが増えれば、せん断に要する力が増加するので、刃欠け(折損)が生じる場合があります。
対策としては、一般的には、 じん性の高い材料を用いるか、刃物硬さを下げてじん性を高める対策を取りますが、これは、耐摩耗性が下がって寿命が短くなる要素の一つになります。
じん性対策とともに、もう一つの大きな問題は、それをせん断する時に発生する「熱の影響」に注目することが必要です。
ねばい(軟らかい)材料を切ると、 切断面の比率が高くなる傾向がありますが、これは、刃物との接触時間が長くなることで、この場合も、刃物に対する負荷が増えます。
ねばい材料でなくても、クリアランスを異常に小さくすると、同様の傾向になります。 このような時に発熱が大きくなるのですが、 これによって刃先が軟化し、摩耗が増加します。
このように、同じ刃物を用いても、被せん断材によって刃物の寿命が変わりますので、被切断材によって 刃物の仕様を変えなくてはならないのは当然ですが、これは、このページの摩耗要素に示したように、多岐にわたっているために、 使ってみなければわからない要素が非常に多いために、刃物を作る場合には困ることです。
6)その他
しばしば、研磨時の表面あらさや残留応力の影響が話題になることがあります。
一般的には、強研磨をすると、表面に引張り応力が残留して刃欠けの危険が増す ・・・とされていますが、これについて、 電解研磨をしてX線解析により研磨後や使用後の刃先の残留応力の変化を調べたところ、当社が行っているような湿式研磨においては、 そのような問題はほとんどないことを確認しています。
このために、普通に湿式研磨している場合には、研磨した製品の残留応力問題は気にしなくてもいいでしょう。
しかし、色が変わるほどの強研削や乾式研磨で品物の表面が高温になりすぎると、 表面に引張り応力が残留しますので注意が必要です。
また、せん断に使用した後の刃先の残留応力についても調査したところ、 摩耗した表面が消えたのち、0.3mm程度追い込んで研磨た状態では、 使用時の残留応力は消失していました。
通常の使用であれば、0.5mm程度を研磨する仕様であれば、 とくに研磨量の不足による問題はないと考えています。
しかし、1000トン以上の 油圧プレスシャーで鉄鋼スクラップ品を切るような刃物では、 3~5mm以上もの深さまでの組織が変質するダメージを受けているものもあります。
また、普通の刃物でも、 両面(刃先すべての刃先面)を研磨しない場合や乾式研磨やバフなどの鏡面研磨、刃先が変形して いるようなもの・・・ などについては個別に研磨量を考える必要があるでしょう。
さらに、研磨砥石の適合性や研磨作業のテクニックなどの基本技術が大切なことは言うまでもありません。
2.刃欠け・チッピング
摩耗とともに、刃欠け、チッピングは厄介なものです。その要因を下表に分類しています。
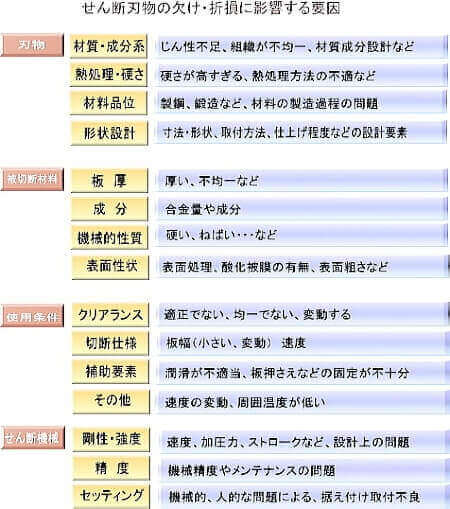
これらが単独、あるいは複合して、刃欠けや チッピング、異常な損耗が発生します。 これらのいくつかについて簡単に説明しますが、原因を特定して対策出来るものは少ない状況ですが、考えられる原因を一つ一つ除去することで高寿命化を考えるといいでしょう。
下図は、打ち抜き工具(上刃はポンチに、下刃はダイスに対応)における力の作用を 示しています。適当な資料がないのでこれを引用していますが、直刃などの刃物は切り離される側の品物が固定されないという根本的な違いがあるので、せん断状況が若干異なった点があります。
1)せん断時の力
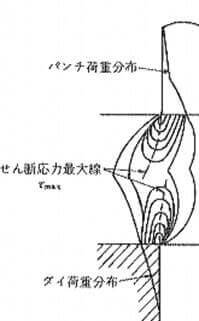
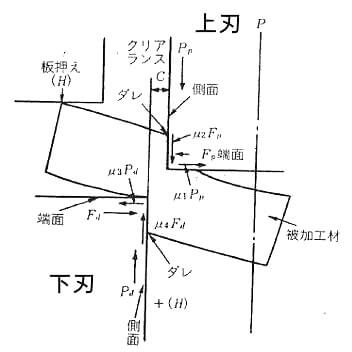
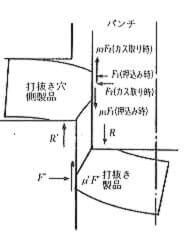
上図で、加圧力は刃先に最も多く加わっています。また、せん断力が刃物面(端面と側面)を押し付ける際に、 摩擦に伴う力が 働いてせん断が 進んでいることが示されています。せん断刃物の場合は、特に、板押さえが不十分だったり、クリアランスが広い場合や被加工材の切離れが遅かったりすると、回転が加わって、余計な力が加わることになります。
下図は、切り終わった状態です。実際にせん断では、加圧力が解放される場合にその反力が加わって、シャーなどに大きな力が加わるのですが、これらの状況は詳しく研究されていません。
引張試験を経験した方はご存知と思いますが、試験片が切り離れたときにすごい音がして引張方向と反対の方向の力が加わっていることを実感できますね。
この図は、上昇過程においても、摩擦力に伴って刃物を押し付ける力が働いていることを示しています。 (もっとも、この ポンチ・ダイスと通常のシャー刃物では若干異なります。シャーでは、シヤー角があり、切り離される板の部分は自由端になっていて、せん断過程でモーメントが加わるなどで若干変わっているところもあるでしょう)
このような力が加わる状況で、刃物が刃欠けしたりチッピングが生じることもあります。
刃物の持つ機械的性質は、被切断材よりもすべて高いとは言えません。 圧縮強度や強さは高いのですが、可塑性や耐衝撃性などは劣りますので、いろんな原因で刃欠けが生じます。
せん断作業をすぐさま 中止しなければならないような「刃欠け」、ときには、 刃物が分断されるような「折損」 などが発生する場合があります。
これらの異常が発生したときには、刃物だけの問題だけをとらえるのではなく、上表の内容を含めて検討する必要があるでしょう。
2)使用初期のチッピング
使用初期に大きな力が加わると、刃先は、その力を分散して受けるように、小さな丸みを形成します。
この時、負荷が小さい場合には、 「摩耗」として徐々に丸みの形成が進みますが、急激で大きな負荷に耐える必要性があると、刃先に小さな欠けが発生して疑似的に摩耗したようにして接触面積を増やして、 せん断時の負荷に耐えるようになります。それを微小チッピングと称します。
下左の写真は、刃先に生じた小さな欠けが連続した状態で、下右側は、それに 比べてやや大きなチッピングを生じて摩耗も並行して生じている例です。(この2例とも、写真の手前の面が刃物の側面で、上側がコバ面です)
このような使用初期の微小チッピングを避けるための方法としては、薄い板から徐々に厚い板を 切るように作業することで徐々に摩耗を進行させ、刃先を滑らかに摩耗させることで刃先の丸みを作って大きな力に耐えるようにすることや、厚板用の刃物などでは、使用前に油砥石を用いて刃先を(心持ち程度に)滑らかにして、使用する前から小さな刃先の丸みをつけておく対策なども行われています。
刃先がなじむまではクリアランスをすこし多めにとることなども有効な場合がありますが、切れ味が悪くなったり、寿命を縮めることも懸念されますので、 切り口を見て、切れ方を判断しなければなりません。
3)刃欠けの様相
「刃欠け」はチッピングと同意かそれよりも大きいものを言います。刃欠けが生じると、切断面を悪くするだけでなく、そのまま使用し続けると、 さらに大きな欠けに進行する場合も出てきます。
刃欠けは、割れの起点(割れが発生した部分)の場所によって、外観から 2つのタイプに分けられ、その成因は全く異なります。
①主せん断力によるものでコバ面、外周面に欠けの起点のあるもの
②側方力などによって、刃物側面に欠けの起点があるもの
①コバ面・外周面に起点を持つ刃欠け
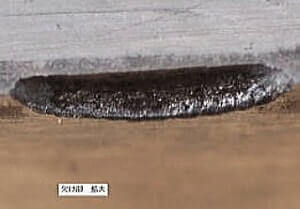
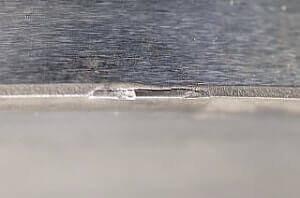
左は「直刃」右は「丸刃」の例です。(適当な写真がなかったので、典型的な 写真ではありませんが・・・)
この欠けは、 (左)摩耗痕の境界に欠けの 起点があり、割れは最終的に刃物側面に達したもので、(右)は、衝撃的な力を刃先に加わった結果と推定されます。しかし、これも推定の域を出ず、多くの場合、刃物側の状況を調べても、原因が見つからない場合もたくさんあります。
この例でいえば、上図にあったように、せん断時に刃先に加わる力は、刃先で最大になっており、刃先から遠ざかるにつれて減少して、摩耗の境界部分で 「ゼロ」になっているはずです。この部分が欠けの起点になっていることは、この部分に大きな引張力が加わていたと考えられます。
圧縮力によって刃物は変形しますが、簡単には圧壊しません。しかし、引張力が刃物の持つ引張強さ以上になれば簡単に刃欠けします。
このために、どうして大きな引張力が生じたのかを調べないといけないのですが、起点近傍で他の部分以上に強度が落ちているとか、 熱影響を受けているとかを、顕微鏡組織や硬さ推移で調べて、何らかの原因を推定出来ればいいのですが、ほとんどどのような確証が得られないものがほとんどです。 ・・・となると、刃物以外の原因になるのですが、その原因によっては利害関係がでることもあって、原因推定は無理なことがほとんどです。
②側面に起点を持つ刃欠け
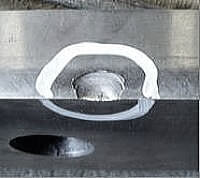
近年は、上記①の「コバ面・外周面からの欠け」よりも、写真のような「側面からの欠け」 が増えています。
これは、先のせん断中に はたらく力に示したように、刃物側面が摩擦されることに起因していると考えられます。
しばしば、使用後の刃物を調べますと、下の写真のように、刃物側面に小さなクラックが 残留している場合があります。(四角錐は、微小硬さの測定痕です)
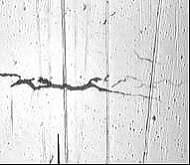
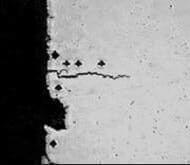
これは、ヒートクラックとよく似ていて、初期には、摩擦方向と直角の方向に発生し、残留しているクラック深さは0.3mm 程度以下です。
この考え方によれば、このクラックは、定常的な加圧中(切断中)の力によって、 それが進行して刃欠けになる可能性は低いのですが、 当然、このクラックが開口する 方向に許容範囲以上の力が加われば刃欠けします。
すなわち、加圧中の側方力がある限界を超えた時に破壊すると考えられるのですが、しかし、これよりむしろ、刃物が離れる (上昇の)際に側方力 (+摩擦力によって刃物を押さえつける力)がクラック部分への 引張り力となって加わることでクラックのくさび効果のために割れが進行し、比較的簡単に 大きな欠けになる・・・と考えるのが適当でしょう。
この負荷に対する抵抗を「破壊靱性」と言いますが、実験値などでは静的負荷について扱うために、運動する(または 応力状態が変動する)場合について適用する場合には、 いろいろな要素について検討しなくてはならず、 これによって簡単に破壊の解析をするのは難しいのですが、破壊の推定をするのには、 破壊靱性の大きさを考えることは有用でしょう。
破壊靱性の大きさは、材質、硬さが大きく 関係し、シャルピー衝撃試験値などとも相関があるとされます。もちろん、それが高いことは破壊しにくいことになります。
さて、この刃物側面にクラックが発生する原因としては、
①せん断面を良くしようとして、 クリアランスを小さくする傾向があること
②切断板の硬さや ネバさが高いものを 切断することが増えて、側方力の増大や切断時の刃物との接触時間が長くなっていること
③シャー側への負担が増えて、 シャーのガタなどが増加しやすく なっていること
・・・など、 いろいろな刃物以外の原因や問題が考えられます。
刃物側の対策としては、
①研削面の仕上げ状態の検討
②潤滑の検討
③被切断材と 刃物の差異の検討
などがありますが、 詳しい説明は別の機会にします。
******
このページの写真の多くは、第一鋼業(株)様の協力で使用させていただいています。
→次の「せん断に関する要素」を読む次のページでは、クリアランスなどのせん断要素について紹介しています。
(来歴) H31.2 見直し R2.4 CSS変更 最終確認R6.4月