脱炭・脱炭層(だったん・だったんそう)[t02]
脱炭とは、加熱中に鋼中の炭素が失われる現象です。
脱炭は、雰囲気と鋼の炭素量の炭素当量の差で生じる場合のほかに、大気中の加熱によって、酸化を伴う脱炭が起こりやすく、熱処理中に進行して、硬さ不良などが起こります。
これは、空気中の酸素が鋼中の炭素と化合してガスとなって飛散して、鋼の表面の炭素濃度が低下するためですが、錆びた鋼を高温に加熱する場合も脱炭が生じます。
表面部で脱炭が生じて炭素量が規定以下になった部分を「脱炭層」といいます。
脱炭の分類
脱炭には、鋼中の炭素がほとんどなくなる(全脱炭・フェライト脱炭などと言う)ものや、拡散脱炭と言われる、雰囲気のカーボンポテンシャル(炭素当量の差)の影響で、鋼の表面から内部に向かって炭素量が低下します。
さびなどに接触している部分でも、脱炭(部分脱炭)が起こります。
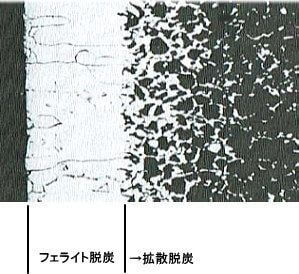
脱炭に対して、雰囲気の炭素が鋼の炭素濃度を上げる場合は浸炭といいます。
脱炭の原因と対策
脱炭は、鋼の表面部分で、加熱中に酸化性雰囲気(大気、水蒸気、酸素など)中の酸素と鋼中の炭素が結合して、鋼中の炭素が一酸化炭素や二酸化炭素のガスとして飛散することで起こる場合が多いようです。
その他、還元性(アンモニア、水素)ガスやソルトバスなどの溶融塩などでも同様の現象が出る可能性があります。
この反応は高温になると進行しやすいので、焼戻しなどの赤熱しない温度ではあまり考える必要はありません。
酸化した品物(さびや黒皮のあるもの)を焼入れする場合には、大気雰囲気以外の無酸化雰囲気であっても焼入れ加熱中に脱炭が生じます。
このため、熱処理の加熱前には、必ず、黒皮や銹(さび)を除去しておく必要があります。(特に、真空炉などで無酸化焼入れする場合は、確実に前処理が必要です)
当然ですが、焼入れのために大気中で加熱する場合には、水分が多いと加熱中に酸化が進行して、それが原因で、さらに脱炭が生じやすくなります。
焼入れなどの高温時に脱炭が生じると、焼入れ後に十分な表面硬さが得られないだけでなく、表面部の応力状態が変わる(焼入れ時に表面が引張応力状態になる)ことで「焼割れ」が生じる原因になります。
脱炭を防ぐ熱処理
脱炭を防ぐ方法としては、雰囲気中の空気を脱気する「真空熱処理」、空気を不活性ガスに置換したり、カーボンポテンシャルを調整したガスを用いる「雰囲気熱処理」、塩浴などで空気に触れないようにして加熱する「ソルトバス熱処理」などがあります。
熱処理する場合は、厳密にいえば、鋼材の成分によって雰囲気のカーボンポテンシャル(炭素当量)を変える必要がありますが、一般熱処理ではそれを常時測定している例は少なく、真空度を高めたり、雰囲気ガス量を増やして、空気中の残存酸素量をさげることや、アルコールや炭化水素系の添加剤を炉中に入れて、脱炭を防ぐ対策をする場合が多いようです。
脱炭(または浸炭)を防ぐためにはカーボンポテンシャルを鋼材にあわせる必要がありますが、浸炭炉などと違って厳密な管理をする機器を備えていない設備も多く、定期的に脱炭検査をしてその限度を確認して日常的に雰囲気を管理しているのが現状です。
これらの脱炭を防ぐようにして行われる熱処理は『無酸化熱処理』と呼ばれます。
また、光輝肌が残るようなものについては「光輝熱処理」と称されることもあります。
(無酸化雰囲気は必ずしも光輝状態で仕上げられるというものではありません)
また、ソルトバス熱処理で使用される塩浴(ソルトの溶融液)についても脱炭しないようにソルトの管理が必要です。
日常的にソルトを使用していると、ソルト中に鉄分が滞留するので、それが加熱中の鋼の表面に付着すると脱炭するため、脱炭に対する日常管理は欠かせません。
その管理の方法として、脱炭防止剤を投入して脱炭しないようにするとともに、成分が既知の鋼箔を用いて塩浴中で加熱したものを検査をして加熱中の脱炭を監視します。
脱炭が生じた場合に、浸炭雰囲気で加熱する「復炭」処理などもありますが、一般的ではなく、通常は、熱処理後に研磨などで、硬さの回復するところまで脱炭部分を加工によって除去しなければなりません。
(来歴)R1.10 文章見直し R2.4 CSS変更 最終確認R6.1月