ソルトバスでの恒温熱処理
ここでは、ソルトバスを使う熱処理のうち、特徴的な「恒温熱処理」について説明しています。
これは、ソルトバスを用いた焼入れ冷却作業で、1100℃程度の焼入れ温度から、約550℃のソルトバスに品物を入れたところの写真です。
このように、ある温度のソルトバスに品物を入れて、その温度に保つ処理が恒温処理です。 この恒温処理には、オーステンパー、マルクエンチ、マルテンパーと呼ばれる処理方法があります。
温度を変える場合はいくつかのソルトバスを用意します
ソルトバス熱処理では、ソルト(混合塩)を溶融して一定温度になったソルトバスをいくつか用意しておいて、加熱したい温度のソルトバスに品物を入れて加熱や冷却をします。
ソルトは気体雰囲気に比べると、比熱が大きく、伝導と対流によって温度の加除をするので、熱による変形を嫌う品物では、加熱時にはいくつかのソルトバスで段階加熱をして、急激な温度差を緩和して熱による変形を防止する方法をとります。(これを予熱といい、加熱には、2-3個のソルトバスを使用します)
ソルトバスでの冷却速度は、窒素ガスによる加圧冷却よりも早く、油冷よりやや遅いという冷却性能です。
(解説) 真空炉などでは加圧冷却することで油冷と同等の冷却速度が出るというものもありますが、強烈な噴流は変形の発生が懸念されるために、通常の作業では、ガス流量を減らして冷却する場合が多いので、ここでは、ソルトバスによる冷却速度は、ガス冷却と油冷の中間だとしています。
ソルトバスでは、油や水などの冷却材よりも温度の高い温度を使って冷却できるところに特徴があります。
たとえば、水では25℃以下、 油では60℃前後において冷却能が高いので、その温度で用いるのが基本になりますが、ソルトバスでは、異なる融点のソルト剤などを用いることで、 150℃から600℃ぐらいの温度で品物を冷却できますので、これによって、焼入れ時の「変態」(組織変化)をコントロール出来ます。
もちろん、現在の最新の加熱炉などでは、マイコンによる冷却速度調整を備える炉もありますが、ソルトバスのような恒温処理を行なうまでにはなっていません。
ソルトバスの欠点は、品物についたソルトバスを除去しなくてはならないことです。
それもあって、ソルト剤を用いない流動層設備や、ホットオイルと呼ばれる、高温の油脂類を用いる方法)などで恒温処理をする方法もあるのですが、あまり一般的な方法にはなっていないようです。
3種類の恒温処理
恒温処理には、「オーステンパー(AT)」「マルクエンチ(MQ)」「マルテンパー(MT)」という3種類について説明されることが多いので、それを図に示すと以下のようになります。
熱処理操作でいえば、焼入れ温度(QTemp)になった品物を、AT、MQ、MTと書かれた温度になったソルトバス中にいれて、 品物がその温度に一定時間その温度に保持したのちに取り出し、 大気中で放冷する操作になります。
このうち、AT1・AT2・AT3に示すものが「オーステンパー」、MQに示すものが「マルクエンチ」、MTが「マルテンパー」と呼んでいます。
この図は、 恒温変態曲線(S曲線)と、連続冷却曲線(CCT曲線)をミックスしたイメージ的な図で、ここではさらに、説明しやすいように、 変態線(Ps・Pf)を意識的に右側にずらした対数目盛にしています。
オーステンパー
この図のAT1、AT2、AT3 などの線が「オーステンパー」処理を表しています。
オーステンパー処理の操作は、パーライトノーズの温度以下の適当な温度で品物を保持して、その後(通常は)空冷しますが、この際に、 保持温度の違いと保持時間の長さによって、軟らかいパーライトにはならずに、ソルバイト、トルースタイト、ベイナイトなどの混合組織が生じます。
写真の左から、パーライト組織、トルースタイト組織、パーライトの拡大組織です。
「パーライト」の拡大組織(山本化学工具研究社の顕微鏡組織から引用:倍率不詳ですが2000倍程度?) で、縦筋の炭化物(セメンタイト)と純鉄成分のフェライトが層状になった組織は、恒温処理の温度が低くなるにつれて、トルースタイト(パーライトよりも細かく、若干硬さも高い組織)や、さらに組織が細かくて硬さが高いベーナイトと呼ばれる組織になっていきます。
それらは層状組織が粗いパーライトに比べて硬さは高いのですが、もっと硬くてもろい、焼入時に急冷してできるマルテンサイト組織とは違って、「オーステンパーでは、ある程度の硬さがありじん性も高い品物になる」・・・というような説明がされていることが多いようです。
このオーステンパー処理をする鋼種は、炭素鋼や低合金鋼などの、焼入性のあまりよくないものがほとんどです。
これは、焼入性が良い鋼種に適用されないのは、変態線が右側に寄って、等温保持する時間が長くなりすぎるため・・・という理由なのでしょう。
上図では、AT1からAT3の3本の線がありますが、これは、保持する温度、保持後の冷却速度などによって、硬さや顕微鏡組織が変わるということを示しています。
これらの条件は鋼種(鋼材の化学成分)で異なるので、求める性質を得るためには、いろいろな実験をして決めます。
このオーステンパー処理は、書籍などでは解説されていることも多いのですが、何がどのようにいいのか・・・などはあまり具体的には紹介されていないのですが、逆に、未知の機械的性質が得られる可能性を秘めている・・・ということかもしれません。
言い換えれば、一般の熱処理には向きませんが、特定の重要機械部品などでは、試してみる価値があるかもしれません。
また反対に、(これは大切なことですが) このオーステンパー処理をすることによって、絶対に高品質のものになる・・・ということではありません。
つまり、 衝撃じん性が高いものが得られたり、熱処理変形が少なかったり・・・という長所ばかりではなく、デメリットとして、必要な硬さが得られない、降伏点が下がる・・・などの予想しなかったデメリットが出てくる場合もあります。
マルクエンチ・マルテンパー
上図の MQ線 がマルクエンチ、MT線がマルテンパーと呼ばれるものです。
一般的に、Ms点直上の温度で保持するのがマルクエンチ、 Ms点にかかる温度で保持するのをマルテンパーといいます。
マルテンサイト変態は温度に依存する変態ですので、品物の温度を均一にしてからゆっくり冷やすことで、変形を押さえつつ十分な硬さを得ることができますから、 結局、マルクエンチとマルテンパーは同じようなもの・・・と考えてもいいでしょう。
以上3つもの恒温熱処理について簡単に示しましたが、ここでは、「このような熱処理をすることも可能で、通常の油焼入れとは違った状態のものができますよ・・・」という程度の内容と捉えておくといいと思います。
ソルトバス熱処理の昔ばなし
このソルトバスによる熱処理は、私の第一鋼業における経験では、1970年代以前からおこなわれていたようで、さびの懸念があったものの、品質的には、お客さんの評判も良かったようです。
昭和年代後期には、SK3、SKS3、SUJ2などで製作された工具や金型部品がおおく、昭和50年代頃からは、それらの鋼種から、焼入性の良いSKD11を使った品物が増えてきた頃でした。
すでに高速度工具鋼の工具も多くあって、それらはソルトバスで焼入れしていたので、ソルトバスは高級な熱処理という感じが強かったようです。
高速度工具鋼は500℃程度、その他の鋼種は160℃程度のソルトバスに焼入れしていました。
当時の鋼材の品位は、現在と比べるとかなり低かったので、油冷や水冷では、しばしば焼割れや大きな変形なども起きていましたので、若干硬さは低くなるものの、焼割れや変形が少ないソルトバス熱処理は結構喜ばれていたのですが、今から考えるとそれらの鋼種のMs点は、(正確ではないかもしれませんが) SK3=160℃ SKS3=100℃ SUJ2=250℃ SKD11=200℃ 程度ですので、熱処理的に考えると、焼割れや変形への効果は、このMs点を見ると、理にかなっていたのでしょう。
この日常的に行われている「ソルト焼入れ」は、上で述べた恒温熱処理とは異なります。現在も、この「熱浴焼入れ」の方法は通常作業として行われています。
例えば、高速度鋼の焼入れでは、オーステンパーなどの恒温処理とは違って、ソルトバスを使用して高速度鋼を焼入れする場合は、500℃程度の熱浴に浸漬し、品物の温度が一定になれば空冷するという熱処理ですし、その他の鋼種でも、180℃程度のソルトバスに入れたあとで空冷しています。
これは「オーステンパー」や「マルクエンチ・マルテンパー」を意識した処理ではないので、第一鋼業ではこれを「ソルト焼入れ」又は「熱浴焼入れ」としていました。
死語になった「アンダーハードニング」
これは、現在では消えてしまっている、1970年頃の熱処理法で、この言葉を聞くことはほとんどありませんが、これは、高速度鋼の焼入れ温度を極端に下げて、1000℃程度のダイス鋼の焼入れ温度程度の低温で焼入れすると、非常に高靱性になる・・・という実験結果があって、その低温焼入れ処理を「アンダーハードニング」と呼ばれていました。
これは、高速度鋼の正規の焼入れ温度よりもかなり低い温度で、共析炭化物をマトリックスに溶け込ませないような、低い温度で焼入れすると、硬さはそんなに出ませんが、非常にシャルピー衝撃値が高いという結果が出る・・・というものでした。
例えば、SKH51(当時はSKH9)の焼入れ温度1200℃程度に対して、ダイス鋼の焼入れ温度程度の1030℃で焼入れすると、衝撃値が1.5~2倍になるのですが、これは200℃程度の低温焼戻しであったために、第一鋼業では、高温特性が劣るので、高価なハイスはもったいない・・・という理由で、このような熱処理はやっていませんでしたが、この言葉の響きは、どこか魅力的であった・・・という記憶があります。
それが消えてしまった理由は、その後に、それ以上の高靱性で耐熱性の高い「マトリックスハイス(セミハイス)」が開発されたためで、それによって、アンダーハードニング処理は文献からも消えてしまいました。
何よりも、高速度鋼の工具の多くは、高温特性が大切なので、高温焼戻しが原則ですので、このアンダーハードニング処理は、忘れ去られていったのですが、しかし、これとは別に、低めの温度で焼入れすることの「良さ」は、知っておいても無駄にはなりません。
例えば、SKH51は1200℃程度で焼入れされるのが普通ですが、それを、1140℃程度の低めの焼入れ温度で、62HRC程度の硬さにして用いたり、SKD11を980℃程度で焼入れすると、シャルピー値は高くなるし、品物によっては、耐衝撃性の必要な工具では、長持ちする場合も多いようです。
これは、硬さを少し下げる事による効果と、結晶粒が大きくならないし、残留オーステナイト量も抑えられる・・・ということにも関係しているのですが、小さなテストピースでは、その理由が明確に出てこないのですが、このようなことも、ソルトバスを使えば、簡単に焼入れ温度を変えることができるので、覚えておいて、実験してみるのもいいかもしれません。
テストピースなど小さな品物での熱処理試験の場合には、極端に焼入れ温度を下げるのはあまりいいことでは無いことが多いのですが、大きな品物になると、短時間加熱は、効果的になることは、多く経験しますので、機会があれば、やって見る価値のあるものもありそうです。 閑話休題。
ソルトバス熱処理は優れているか?
幾度か書いていますが、ソルトバスの長所は、品物にあった熱処理ができることですが、それが最適な熱処理になっているかどうかは別ですので、「ソルトバスは優れている」というのは、若干無理があります。
しばしば(社内でもお客様からも)「窒素ガスの加圧冷却による炉(真空炉など)で焼入れした品物よりも、ソルトバスで熱処理した品物のほうが工具寿命が良い」 と言われるのを聞きますが、これも、しっかりと評価されたものではありません。
私は、ソルトバスは小さな設備なので、一つ一つの品物に合わした熱処理条件で作業できる強みと、真空炉などのバッチ処理と異なり、品物のあった加熱時間をとることができる熱処理法であることで、焼入性のあまりよくないハイス類や 刃先の鋭利なナイフなどの工具類では、その価値は高い・・・と考えているのですが、それでも、熱処理品質に及ぼす要因はさまざまなものがありますので、いずれも、比較検討してじっくり考える必要であるのはいうまでもありません。
ソルトバスは熱処理実験に向いています
ソルトバスの長所は、恒温熱処理ができるというだけではなく、最大の特徴は、加熱温度、加熱時間、冷却方法を、その品物に応じて、簡単に変えることができる点にあります。
もちろん、ソルト中で加熱したものをソルト中にいれて焼き入れるのではなく、ソルトバスから取り出して、水焼入れや油焼入れすることも可能ですし、数個、数十個のテストピースでも、焼入れ温度を少しづつ変えて熱処理する・・・・などの、ふつうの加熱炉では大変なものでも可能ですので、熱処理実験には最適です。
ソルトバスは消えゆく運命にあります
ソルトバスの熱処理では、サビの発生やソルトの洗浄除去などが問題で、人手がかかり、生産性も低いので、いくら熱処理特性が良くても、しだいに消えゆく運命にある設備です。
第一鋼業の設備も、現在は航空機部品の熱処理品で必要なものですが、それらが、真空炉による熱処理仕様に変わっていけば、処分されるのは間違いありません。
そうなると、オーステンパーやマルクエンチなどの恒温処理で用いられている熱処理用語も、死語になってしまいます。
ソルトバスは熱処理実験が安価に短時間でできるので残ってほしい設備ですが、企業である限りは、設備が消えるのは仕方がないでしょう。
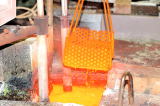
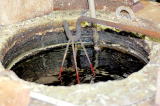